28 mins read
A Complete Guide To Efficient Subcontractor Management
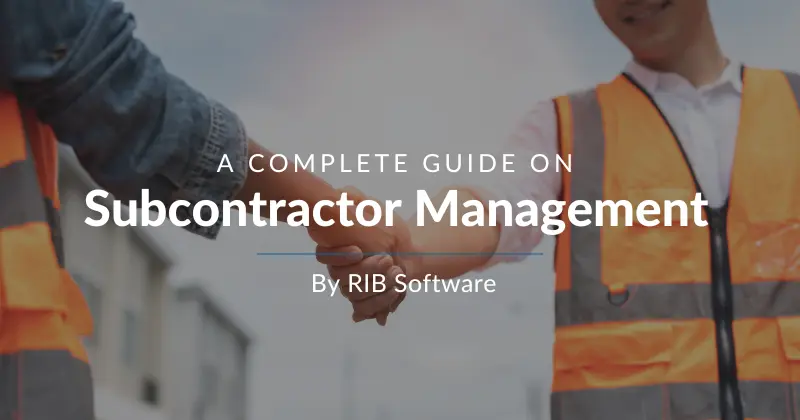
In the construction, mining, and industrial sectors, subcontractors are essential in delivering a project on time and within budget. Engaging and employing subcontractors for the appropriate tasks is a priority for main contractors, particularly when the job demands multiple specialized subcontractors’ appointments.
Subcontractors are responsible for helping general contractors complete their projects on time and within budget. From enormous builds requiring large-scale resources, to smaller ones that call for specialized skills, a subcontractor is engaged whenever a main contractor lacks the resources or expertise to complete a particular aspect of a job.
This RIB blog post will explore the art of construction subcontractor management and how the proper best practices and tools can ensure subcontracting success. Let’s dive in!
What Is Subcontractor Management?
Subcontractor management is the process of procuring and managing subcontractors on a client’s behalf. In construction projects, the contractor is usually responsible for managing subs with specialized software support to achieve expected results.
That said, managing construction subcontractors is about more than just hiring and monitoring. The process is much more complex and involves various activities, such as construction bid management, contract administration, and compliance.
The subcontractor management process happens in four stages, where the activities we just mentioned occur. These stages include:
- Pre-award: At this stage, the general contractor (GC) studies the project needs and sends requests for quotations (RFQs) and requests for proposals (RFPs) to procure the subcontractors needed.
- Award: At this stage, the GC reviews the bids from subcontractors and selects the ones that best suit the project’s needs. The GC then negotiates contract details and requirements under which the subcontractor will work.
- Post-award: This stage occurs after the project has started. Here, the GC monitors subcontractors to ensure they perform their tasks according to the expected quality and timeline.
- Close-out: As its name suggests, this happens during the final stages of the project. The GC carefully inspects the work carried out by contractors and issues change orders if they are not happy with the result.
Who Manages a Subcontractor?
As you probably gathered by now, subcontractors don’t deal directly with the project owner or client. The general contractor is responsible for managing subcontractors. The GC must ensure subcontractors are aligned with the project’s general goals and objectives and the expected quality and safety standards. This is often measured using interactive construction reports containing real-time progress data about performance.
Other construction roles that play a role in managing subcontractors include the project manager, who ensures subcontractors have the necessary resources, materials, and information to complete the work, and the construction manager, who supervises them on-site, making sure that safety regulations and other requirements are respected. In less common cases, mainly for large firms, a dedicated subcontractor manager is appointed to deal with all aspects of subcontracting.
Types of Subcontractors in Construction

A successful construction project is a team effort. It is almost impossible for the GC to bring the project to life without the help of some specialty contractors, also known as subcontractors. These professionals manage specific areas of the construction process that require more expertise, such as:
- Site preparation: As its name suggests, this type of specialized contractor is in charge of preparing the site for construction. This means bringing equipment to remove trees, level the property, and excavate for the foundations. In smaller projects, the GC might take care of this step themselves.
- Concrete: This professional oversees anything that requires concrete, such as foundations, slabs, or a parking lot. In many cases, this contractor brings precast concrete parts, such as beams, walls, or stairs, to make the process more efficient.
- Structural and framing: This specialty contractor installs the building’s structural components. The structure and framing might be wood, steel, or concrete, depending on the project.
- Roofing, siding, and sheet metal: This specialty encloses the building and protects it from damage from the exterior, such as varied weather conditions. These contractors often use prefabricated materials, making their work faster and more efficient.
- Carpentry and flooring: Specialized carpenters take care of interior finishes like cabinetry, doors, floors, and other decorative woodwork details.
- Heating, ventilation, and air conditioning (HVAC): This specialty manages the climate inside the building. HVAC contractors usually install air conditioners, boilers, furnaces, and other equipment to ensure the climate inside the structure is safe and comfortable for occupants. In some cases, HVAC contractors might also take on plumbing and gas-related work.
- Electrical: These contractors are responsible for all electrical work in the building and construction site. They install electrical panels, wires, generators, fire and burglar alarms, and other equipment. They are often certified and have specialized permissions to install these types of equipment.
- Plumbing: This contractor installs and maintains quality plumbing systems. Some common activities include drainage system installation, water pump installation, and water system balancing.
- Drywall: These professionals are in charge of installing drywall on the framing of walls and ceilings. In case of renovations, they oversee repairing any issues related to drywall.
- Painting and paper hanging: As its name suggests, this subcontractor is responsible for painting interior and exterior surfaces with great precision and attention to detail. Their process includes masking, sanding, priming, and caulking to leave the surface ready for painting. They are also in charge of installing wallpaper if needed.
- Landscaping: This contractor is responsible for bringing the building to life by eliminating any damage caused during construction, designing gardens and walkways, and adding attractive accents to the landscape.
The Importance of Efficiently Managing Subcontractors
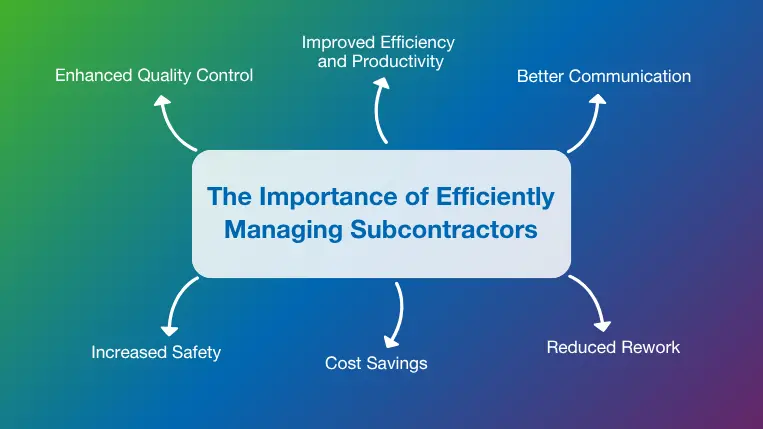
Construction projects involve many moving parts and people that must be managed efficiently to minimize issues, delays, and cost overruns. Subcontractors are a fundamental part of this machine and can significantly affect the project’s result if not managed correctly.
A well-thought-out subcontractor management system will ensure your projects cost less and take less time to be completed. All aspects of the relationship will be managed beforehand, preventing any issues or delays due to misunderstandings, which means there will be fewer risks to mitigate. Other benefits include:
Enhanced Quality Control
One of the most important objectives of subcontractor management is safeguarding project quality. Establishing clear lines of communication and responsibility, working with subcontractors to solve problems proactively, and providing necessary training and onboarding support are among the most effective ways to accomplish this.
GCs managing subcontractors can also establish metrics and construction KPIs to baseline progress and identify areas in need of improvement. Some contractors also choose to implement rewards and incentives for subcontractors who meet or exceed expectations, but equally positive results can come from establishing trust and promoting teamwork.
Improved Efficiency and Productivity
Inefficient or unproductive subcontractors can reflect badly on the general contractors who selected them, and create unwanted problems when schedule or budget adherence is jeopardized. To prevent this scenario, subcontractor responsibilities should be fully understood and conveyed so they can understand exactly what needs to be done and when it needs to be completed.
With a clear line of sight to project leadership, the general contractor can also prevent scheduling conflicts and delays that impact productivity by coordinating the timing of operations and resource utilization. Clear expectations and consistent monitoring create a winning formula for optimizing productivity on the job site.
Better Communication
Improved communication is one of the most important benefits of the subcontractor management process, since clear lines of communication between all GCs and subcontractor teams contribute to smoother project execution while making each individual feel more valued and trusted. Well-defined contracts set the stage for effective communication early on, with documents used to communicate project objectives as well as timelines and payment terms. Periodic meetings with subcontractors should be used to exchange information and ideas while making the larger team aware of any new safety issues, risk factors, and other important topics that might otherwise remain unknown.
Reduced Rework
Excessive rework can undo any previous quality, productivity, and communication benefits, so an effective subcontractor management plan should also focus on preventing or reducing rework whenever possible. For example, GCs should continuously collaborate with drywall installers to ensure the correct material type and installation patterns are being used, and any workmanship or training issues are rectified as soon as possible. This same level of diligence and follow-up is required for each trade and task. Rework is also minimized when work order changes are communicated to subcontractors quickly through digital or in-person communication channels.
Cost Savings
Subcontractor management in construction is also an effective way to reduce costs. The efficient scheduling, minimized downtime, and reduced rework that come from improved oversight and communication directly impact the bottom line. GCs can also reduce costs by evaluating bids and awarding contracts based on a combination of competitive quotes and subcontractor vetting, so that both profitability and quality are ensured. As projects near completion, organized progress reports and subcontractor records help to mitigate any potential conflicts that can impact profitability or damage important relationships.
Increased Safety
Employee health and safety should be the top priorities on every jobsite, and robust subcontractor management helps to make this a reality. This begins with the proper vetting of subcontractors to review their safety records and history, and continues through training programs, personal protective equipment (PPE) issuance, and documented protocols that make safety responsibilities and expectations clear.
Even with these precautions in place, regular site inspections and technology integration help to verify safe conditions in areas that only specialists frequent. The growing list of technology options includes IoT (Internet of Things) sensors to monitor building and environmental conditions remotely, and mobile-friendly software to issue and receive real-time safety alerts and warnings.
Common Subcontractor Management Challenges
The benefits of subcontractor management are balanced by common challenges that can be difficult to overcome. Since general contractors are not able to perform all the work themselves, they must entrust many essential and time-sensitive tasks to subcontractors, and in some cases, work with these specialists for the first time. This creates a level of risk for GCs that can only be minimized through effective monitoring and management. Additional challenges of subcontractor management include:
Coordination of Multiple Contractors
The challenges of managing subcontractors are multiplied by the number of individual specialists, with each having their own work styles, communication habits, training levels, and experience. This means the GC must adapt their management style for each situation, while also setting common expectations and requirements that all subcontractors must adhere to. Direct communication between subcontractor teams is to be expected, but the GC must also stay in the loop to prevent any unintended quality or schedule issues.
Overallocation of Resources
The goal of construction project managers and general contractors is to estimate resource requirements accurately early on, so that the bids and estimates submitted by subcontractors align with these expectations. Unexpected delays, scope changes, lack of visibility, and compressed schedules can easily alter these expectations, putting too much pressure on subcontractors to complete tasks quickly. Planning for contingencies and backup resources helps to alleviate the time pressure on subcontractors.
Licenses and Insurance
General contractors typically do not carry subcontractors on their insurance policies, but they are responsible for ensuring that subcontractors have the appropriate licenses and insurance policies in place for each project. The potential legal and reputational consequences of employing uninsured contractors make this a key point of emphasis during the vetting process, and the validity of all documentation should be thoroughly verified. Cloud-based subcontractor databases can be helpful in maintaining this information over time and accelerating the qualification process.
Fluctuating Labor Costs
The ongoing labor shortage in construction can make it difficult to find workers and subcontractors when and where you need them, especially in remote areas or regions with high seasonal demand. The competition for workers can quickly impact labor costs, making it difficult to price new tasks based on historical labor rates. Escalation clauses and flexible staffing strategies are two common methods GCs use to prevent labor rate spikes from eating into their profit margins.
Change Management
Changes to the project design, scope, or schedule are a part of normal operations, but they also complicate subcontractor management when the timing and coordination of trades and tasks are impacted. For example, an electrical system change during the project might call for additional resources and time, and this can create a domino effect that disrupts or delays the timing of specialized carpentry, insulation, and painting tasks that follow. Each change also becomes a potential source of communication, material, and training issues that must be addressed to keep subcontractors aligned and engaged.
How To Manage Subcontractors? Tips & Best Practices

Now that you know what this process is all about and how it can benefit your projects, let’s examine some tips and best practices for ensuring successful subcontractor management and boosting construction productivity.
1. Define your subcontracting needs
Like any other construction process, a subcontractor management plan starts with efficient planning. This means thoroughly analyzing the project to identify the need for additional workforce or specialized trades. Doing so will help you begin the construction bidding process with a clear idea of what you need, avoiding wasting resources to figure it out as you go.
2. Pre-qualify contractors carefully
Once you have identified the project’s needs, it’s time to pre-qualify potential subcontractors. To source the best candidates, evaluate key factors like past performance, safety ratings, financial stability, and, most importantly, experience level in the project context. Some of these things can be easily learned by asking for references from prior clients to get an idea of performance. This process should also be considered for subcontractors you have worked with in the past as their certifications might have expired or key team members may not be available anymore.
Another good practice when pre-qualifying subcontractors is soliciting at least three bids per trade. This will ensure you have a clear idea of the available options and choose the one that best fits the project’s timeline and budget. Doing so also encourages bidders to offer competitive proposals to win the project.
3. Define contracting details
We mentioned that managing subcontractors starts in the pre-award stage. This is when your subcontractor management system should really begin to shine. Contract negotiations will define the relationship between the GC (in representation of the client) and subcontractors for the project’s entire duration. Therefore, any agreements, responsibilities, deliverables, and rules should be put in writing to avoid issues in the future. This includes payment terms, timelines, mechanisms to resolve potential disputes, safety measures, and much more.
Defining expectations clearly from the beginning will prevent misunderstandings that can lead to project delays or legal issues with subcontractors, ensuring they effectively play their role in the project.
4. Identify potential risks or scheduling issues
As an extension of the previous point, when managing subcontractors, it is important to identify potential risks or scheduling issues that might affect the project later. Common risks related to subcontracting can include delays and quality or safety issues, among other things. Some of these challenges can be addressed during the bidding process to automatically discard subcontractors who are too risky. Other potential risks, such as scheduling issues, can be discussed during contract negotiation or follow-up meetings. For example, the GC can call for a meeting with all trades to organize the timelines. Tasks are sometimes given a couple more days than they would typically require, creating room for error and delays.
5. Set clear communication channels to boost collaboration
This is probably the most important best practice you can follow for a successful subcontractor management plan. Communication in construction has been a challenge for decades. With so many moving parts, a project will simply not succeed if all parties are working separately, which makes setting clear communication channels a priority.
The GC should keep subcontractors constantly informed about project progress, new developments, or unexpected changes. This will boost a spirit of teamwork that will encourage subcontractors to work together with the GC, offer ideas and solutions to issues based on their expertise, and bring the project forward.
Professional construction document management software offers the perfect environment for collaboration and communication with the ability to share important documents and information in real time. This ensures everyone remains connected and works from a single source of truth.
6. Evaluate subcontractors regularly
Another tip for managing subcontractors efficiently is to measure their progress and performance in real time. To do so, the GC must rely on construction analytics software to generate reports and track metrics that will provide valuable insights. These performance evaluations should be carried out regularly throughout the project. This lets you promptly provide necessary feedback and prevent potential challenges from becoming bigger issues.
7. Establish key performance indicators (KPIs)
As mentioned above, software tools simplify the process of monitoring and reporting metrics to subcontractors; however, establishing a short list of important metrics and performance targets helps keep the focus on the most critical issues. The key performance indicators (KPIs) will vary for each project and trade, but metrics like schedule performance index (SPI), on-time delivery, and cost variance (CV) help to identify trends that must be addressed quickly.
KPIs can also be applied to quality metrics like defect rates, especially when these defects lead to costly rework or potentially unsafe conditions. In other instances, material waste gains importance for the overall health of the project. For example, tile setters, carpenters, and welders utilize their skills, training, and experience to prevent excessive breakage or material waste.
8. Conduct site visits
When managing subcontractors in construction, there is still no substitute for regular site visits to inspect work in person, collaborate on upcoming tasks and issues, and highlight the importance of the work each specialist performs. While GCs are not always experts in each individual trade, their presence on site provides another set of eyes to detect non-compliance or safety issues while giving direct feedback on the quality and timeliness of the work. Site visits also improve insight into the overall conditions and challenges faced by subcontractors, including any equipment, environmental, or material storage and handling constraints the GC was not previously aware of.
9. Document all activities
Handshake agreements and trust still have value for subcontractor management in construction, but it is also important to keep complete records of all subcontractor activities, including progress reports, safety documentation, and financial records. Thorough record keeping is the key to avoiding misunderstandings and disputes, while creating a paper trail for any future audits or litigation that arise after subcontractor tasks are completed.
Diligent construction documentation management also benefits subcontractors when they track expenses and deviations in real time to ensure fair payment will be received. This history provides valuable inputs for future bids and estimates, while making the justifications for any delays or overruns more accessible.
10. Ensure timely payments
Like all businesses, subcontractors rely on timely invoice payments to meet their own obligations and keep their teams intact. Efficient payment processing promotes positive relationships while eliminating disputes or delays due to financial issues.
A smooth process begins with payment terms that are clearly defined and agreed upon in the contract, and accounting tools and software capable of processing and tracking invoices quickly and preventing underpayments and other errors. While getting payments to subcontractors on time is important, it is also essential to comply with the specific tax withholding and documentation requirements for invoice payment in each region.
What Can Subcontractor Management Software Do for You?
Lacking information at the right time or in the appropriate format can severely impact a contractor’s ability to perform and deliver projects. However, the operational challenges posed by the complexity of these tasks can be addressed with the right technology.
Using an integrated system that inherently understands the complexity of managing subcontract life cycles can positively impact contractors’ operational efficiencies and bottom lines.
RIB Candy and RIB BuildSmart software were designed for precisely that purpose. Combining project control and fully integrated enterprise management, these solutions work together to offer seamless and flexible subcontractor management, covering life cycle highlights such as adjudication, contract award, progress, certification, and final account.
There are several benefits for managers or supervisors overseeing subcontracts through such integrated systems:
- Item tracking: Through the subcontractor management module within RIB Candy, items from the main bill of quantities (BOQ) can be isolated to create a separate subcontractor BOQ with its own awarded rates. Subcontractor BOQs can also be linked with those of clients to ensure more manageable cost and budget comparisons.
- Legal compliance: A specialized system can help ensure compliance in terms of payment notifications and other processes, such as the local nuances of remittance. This is an immensely important feature in markets like the UK or Australia.
- Variation orders: Industry-specific technology such as RIB CanBuild allows contractors to track changes and variations clearly and concisely. RIB BuildSmart also helps to streamline processes through real-time data entry and field solutions, effectively allowing contractors to navigate the complex world of variation orders with a simple, easy-to-use platform. The detailed and accurate records it helps to maintain, in turn, ensure that payment delays do not affect the project or its subcontractors.
- Tracking progress: With resource planning platforms that understand contractor requirements, the contractor’s project teams can monitor and manage subcontractors at an operational level. For instance, RIB Candy’s direct, unique integration with RIB BuildSmart allows finance departments to track certificates, advances, retentions, and on-site materials in real-time, allowing contractors to do more with less.
- Streamlined management: Contractors that typically engage multiple companies for several projects at a time need the ability to digitally manage obligations, subcontractor progress, and cash flows. An effective subcontractor management system can help projects, and package managers or supervisors track progress on every parcel at a granular level and ensure each project meets its planned deadlines.
Final Thoughts
As you learned throughout this guide, efficient subcontractor management is fundamental to the success of your projects. Whether coordinating timelines, measuring performance in real-time, or ensuring that legal requirements are met, managing subcontractors is fraught with challenges. However, establishing processes to ensure effective communication, quality, and safety can streamline the project and significantly reduce rework, delays, and cost overruns.
Using specialized construction software, such as RIB Candy and BuildSmart, is the most effective way to manage subcontractors. Having a single source of truth eliminates duplication, creates data integrity, and avoids errors – all familiar consequences of managing subcontractors manually using platforms such as MS Excel.
Recording, storing, and managing this data digitally means previously complex reviews, such as subcontractor costs and performance per contract, become easier, faster, and more accurate. These systems also help to dismantle traditional workplace silos and ensure that the deeply insightful data produced by contractors is shared in uniform and easily understandable formats across all levels of the business, where required and with controlled access rights.
Access to real-time, accurate data is essential for management teams in the construction, mining, and industrial sectors to make informed, fact-based decisions that grow their business.
RIB Software is inherently built to support this ease of decision-making. If you are ready to experience all the benefits mentioned above, get a demo for RIB’s toolkit today!
Most Recent
28 mins read
27 mins read
24 mins read
25 mins read
Blog Categories
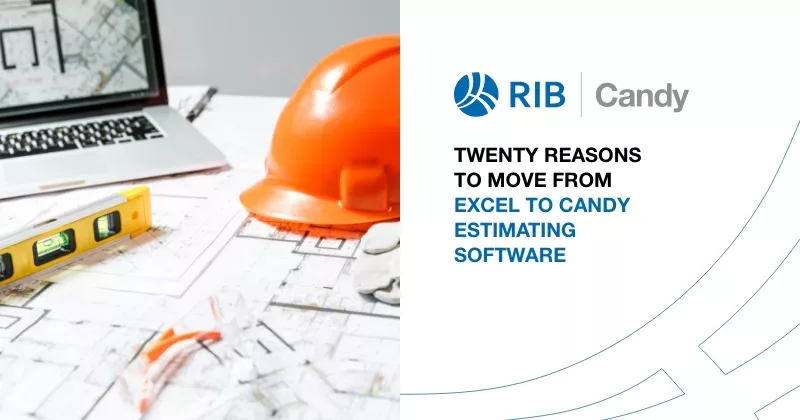
Ebook