28 mins read
How Precast Concrete Is Driving The Demand For Smart Factories
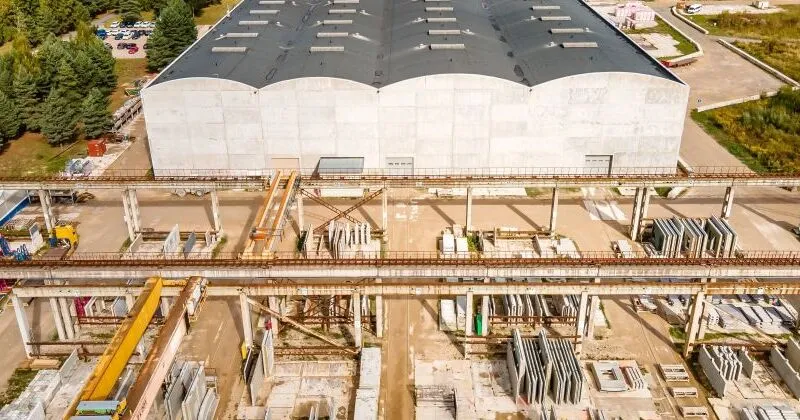
- What is Precast Concrete?
- Precast Concrete Manufacturing Process
- Advantages of Precast Concrete
- Types Of Precast Concrete
- What Is A Smart Factory?
- Technologies Used In Smart Factories
- Advantages Of Smart Factories
- The Rise of Smart Factories
- Smart Factory Systems for Precast Concrete
- What Is Next For Precast Concrete and Smart Production Facilities?
- Conclusion
The surge in demand for precast construction has spurred an increase in the utilization of advanced manufacturing technologies and processes to fabricate these elements. These advanced manufacturing technologies, known as ‘smart factories,’ use digital technologies such as automation, robotics, IoT (Internet of Things), data analytics, and AI (Artificial Intelligence) to optimize production processes, improve efficiency, and enhance product quality.
Smart factories integrate these technologies into every aspect of precast production, from design and planning to fabrication and assembly.
In this post, we look at the precast process, its advantages, and key types. We also explore how smart factories are adopting a modern approach by leveraging Industry 4.0 to enhance efficiency, productivity, and flexibility in the manufacturing process.
What is Precast Concrete?
Precast concrete is a construction material produced by casting concrete in a reusable mold or form, typically in a controlled factory environment. The concrete elements are then cured and hardened before being transported to the construction site for installation.
This construction method contrasts with traditional cast-in-place concrete, where concrete is poured and cured on-site.
Precast concrete has seen more widespread adoption in recent years because of its advantages, including improved durability, quality control, design flexibility, quicker build timelines, the ability to create standardized, high-quality components, and minimize waste.
It is used in various residential and commercial construction applications, including producing beams, columns, walls, slabs, and other structural components.
Precast Concrete Manufacturing Process
The precast manufacturing process involves several key steps:

Precast elements are created by pouring concrete into molds or forms designed to the final product’s desired shape and specifications. These reusable molds can be made from various materials, such as steel, fiberglass, or rubber. The first step in manufacturing is to start generating molds based on the client’s requirements and the precast concrete design.
2) Reinforcement
Reinforcement materials such as steel bars (rebar) or mesh are often placed within the mold before concrete is poured to enhance the structural strength of the precast elements. This reinforcement adds strength to the concrete, making it more crack resistant.
3) Pouring Concrete
Once the molds are prepared, concrete is poured into them. The concrete mix is carefully formulated to meet the project’s specific requirements (including strength, durability, appearance, etc.).
4) Curing
After pouring, the concrete is left to cure and harden within the molds. This process typically occurs in a controlled environment, such as a curing chamber, to ensure optimal conditions for the concrete to reach its desired strength.
5) Demolding
Once the concrete has sufficiently cured and achieved the desired strength, the precast elements are removed from the molds. This marks the completion of the precast manufacturing process in the controlled factory setting.
6) Stockyard Management
Some companies may need to store precast elements before transporting them to the construction site, so efficient stockyard management is critical, especially for larger companies with extensive storage areas. Barcode technology simplifies location tracking of the precast elements within stockyards. This not only reduces errors but also improves the speed of retrieval and increases record-keeping accuracy.
7) Transportation and Installation
When needed, the finished precast elements are transported to the construction site. Installation is often faster and more efficient than traditional methods, as the precast elements are ready for use on arrival.
Advantages of Precast Concrete
Now that you know what precast concrete is and how it is manufactured, let’s explore some advantages your business can reap from using this technology.
Utilizing precast concrete can significantly impact the entire construction project lifecycle, from the initial preconstruction planning phase to the build phase, all the way through building operations and maintenance. Let’s unpack the advantages throughout the different phases of the construction lifecycle:
▷ Planning and Preconstruction
Early involvement of precast manufacturers in the design phase facilitates construction collaboration between different stakeholders, leading to efficient planning and more cost-effective solutions. Precast concrete also allows for a high degree of design flexibility, enabling architects and engineers to create diverse and intricate structures. Using precast elements can accelerate construction schedules, which teams can factor in as they develop project timelines.
▷ Build Phase
The build phase benefits from the speed and efficiency of precast elements, significantly reducing on-site building time. It also reduces the need for extensive on-site labor, addressing potential labor shortages and improving construction site safety. Additionally, using digital construction tools for tracking crews, managing logistics, and planning element stacking enhances the overall operational efficiency of a project.
▷ Building Maintenance and Operations
Precast concrete is known for its durability and resistance to environmental factors. It contributes to the structure’s longevity and reduces the frequency and cost of maintenance and repairs. It can also contribute to a building’s energy efficiency and provide thermal mass and insulation that helps regulate indoor temperatures and reduce energy consumption.
Types Of Precast Concrete
As precast concrete grows in popularity, several products have been developed to make building projects more time—and cost-efficient. Below, we will discuss the main types of precast concrete products to keep putting the value of this technology into perspective.
Before we discuss the types, it is important to note that precast construction products are categorized into standard and special. Standard products are shaped items that can be mass-produced, while specialized products are specially built to meet the needs of a building structure.
Now, let’s explore the types of precast concrete products!

- Precast Concrete Steps & Stairs
Construction companies can order precast concrete steps by unit or complete staircases with flights and landings. These products come with pre-installed treads and risers, so they are pretty intuitive and quick to install.
Stadiums and arenas use precast concrete steps to speed up the building process. The same is true for pedestrian ramps or dressing rooms, which use other types of precast concrete products.
- Precast Concrete Walls
These are large, often rectangular-shaped, concrete panels that can be used to create exterior or interior walls. They come in varied sizes with high reinforcement and can be designed to meet project needs.
One of the most significant advantages of using precast walls is the considerable time savings it provides to projects. This is because the premade walls can be manufactured simultaneously while the site foundations are being built.
- Precast Concrete Beams
Precast concrete beams provide structural support to buildings or infrastructure. There are two types of precast beams: internal ones for when the floor loading is approximately symmetrical and external ones for when the floor loading is predominantly symmetrical. Like walls, these are designed in different shapes and sizes to meet the project’s needs.
- Precast Concrete Columns
Precast columns are usually continuous to the total height of the building. However, if a building is over five stories, two or more columns are spliced to complete the structure. There are three types of precast columns: edge columns that are symmetrical in one direction, internal columns that are symmetrical in all directions, and corner columns that are not symmetrical at all.
These columns can be erected five times faster than regular concrete columns, making the process much more efficient and less expensive, as less labor is required on site. Additionally, the erection process is completely silent, meaning it can happen at any time of the day or night.
- Precast Concrete Slabs
Precast slabs are used for a number of purposes in a construction project, such as stairs or ceilings. They don’t come in standard sizes and shapes; the dimensions are specific to the client’s requirements.
Although they are designed to withstand heavy loads, precast slabs are usually manufactured in long, thin sections that are quite easy to transport to the construction site.
Additional applications of the types of precast concrete mentioned above include piles and decks for railroad and highway bridges, burial vaults, and commercial buildings such as hospitals, malls, airport terminals, and much more.
What Is A Smart Factory?
A smart factory is a digital manufacturing facility that uses technologies such as AI and IoT, machines, and systems to extract data and improve the production process through automation. Smart factories are a part of the technological transformation known as Industry 4.0.
The rise of smart factories came after decision-makers realized that the manufacturing and supply chain industries urgently needed to undergo a digital transformation. The process was even more rushed after the pandemic highlighted supply chain inefficiencies that needed to be solved immediately if companies wanted to remain competitive. This, paired with the increased demand for faster deliveries from the consumer side, drove the manufacturing industry into this big transformation.
But how did they do it?
Technologies Used In Smart Factories
Smart factories can utilize a number of technologies, including:

▷ Automation and Robotics
They integrate automation and robotics into the production process. This includes robotic arms and machinery to automate tasks like concrete mixing, casting, and demolding. These technologies not only accelerate production timelines but also enhance the quality and consistency of precast elements.
▷ Laser Systems and MES Solutions
Integrating laser systems in precast digitalization plays a crucial role in ensuring precision and reducing errors. These systems, forming part of Manufacturing Execution Systems (MES), capture the geometry of precast elements with high accuracy, eliminating manual measurements and enhancing overall productivity. The MES solution, including quality management modules and advanced cameras, facilitates real-time quality control by overlaying CAD designs onto the actual precast elements.
▷ IoT (Internet of Things)
Sensors and connected devices can be embedded throughout the production facility to collect real-time data on various parameters. These sensors can monitor factors like temperature, humidity, concrete curing times, and equipment performance. The data collected is then analyzed to optimize production processes and predict maintenance needs.
▷ Digital Twin Technology
Digital twin technology creates a virtual replica of the physical precast concrete elements and the entire manufacturing process. This allows for real-time monitoring, analysis, and simulation, enabling manufacturers to identify potential issues and optimize production without disrupting the actual manufacturing process.
▷ Artificial Intelligence (AI)
AI algorithms can be employed for quality control, predictive maintenance of machines, and optimization of production schedules. Machine learning algorithms can analyze historical data to identify patterns and trends, helping improve the efficiency and quality of precast concrete manufacturing.
▷ Advanced Materials and 3D Printing
Smart factories may explore using advanced materials in precast concrete production, including those with enhanced durability, strength, and sustainability. 3D printing technologies may also be incorporated to create intricate and customized precast elements.
Let’s continue exploring smart factory technology with some key benefits, as shown below.
Advantages Of Smart Factories
The rapid pace of technological advances creates seemingly limitless possibilities for the AEC space. As we work to build more efficiently, durably, and sustainably, we’ve seen increased interest in precast concrete building and smart factories.
The digitalization that smart factories deliver not only helps to streamline the manufacturing of precast components but also provides a host of other benefits in the process. These include:

▷ Increased Efficiency
Automation and robotics streamline production processes, reducing manual labor and significantly speeding up manufacturing cycles. Additionally, using 3D data reduces the need for manual measurements, improves quantity takeoff and estimating accuracy, and contributes to overall efficiency.
▷ Improved Quality Control
Digital technologies, such as sensors and real-time monitoring systems, enable precise quality control throughout the entire production process. This results in consistently high-quality precast elements, which minimizes defects and rework.
▷ Cost Savings
Although the initial cost of using precast concrete may be higher, optimized resource utilization, minimized waste, and long-term benefits such as reduced maintenance and operational costs can result in overall cost savings throughout the building’s life cycle.
▷ Enhanced Customization
Digital technologies like Building Information Modeling (BIM) and digital twins allow for greater design flexibility and customization. Smart factories can efficiently produce diverse precast elements tailored to specific project requirements.
▷ Sustainable Practices
Smart factories often incorporate sustainable practices, including using recycled materials, energy-efficient processes, and reduced waste generation. The longevity of precast structures also contributes to sustainability by reducing the need for frequent replacements.
▷ Predictive Maintenance
IoT sensors and data analytics enable predictive maintenance, identifying potential issues in equipment before they cause disruptions. This minimizes downtime, extends the lifespan of machinery, and ensures continuous production.
▷ Real-time Monitoring and Control
With the integration of Industry 4.0 technologies, smart factories provide real-time visibility into the production process. Manufacturers can monitor key metrics, adjust parameters, and make informed decisions promptly, leading to optimized operations.
▷ Workplace Safety
Automation takes over many labor-intensive and hazardous tasks, improving overall workplace safety. Human workers can focus on more skilled aspects of the manufacturing process, reducing the risk of accidents.
▷ Supply Chain Integration
Smart factories are often connected to a digital supply chain, allowing seamless coordination with suppliers, construction sites, and other stakeholders. This integration ensures the timely delivery of precast elements and facilitates efficient project management.
▷ Data-driven Decision Making
Data collection and analysis from various production stages enable data-driven decision-making, which leads to continuous improvement in processes, product quality, and overall operational efficiency.
The Rise of Smart Factories
Recent challenges have created a shift in the AEC landscape, so while the industry has historically been slower to adopt new technologies, we’ve seen a recent boom in technology investment. An estimated $50 billion was invested in AEC tech between 2020 and 2022, 85 percent higher than the previous three years. From AI to automation and robotics to project management software, firms have plenty of options regarding technology adoption. Here, we’ll look closer at how advanced technologies can be used to create smart factories highly digitized and interconnected production facilities.
Smart Factory Systems for Precast Concrete
Factories can be set up with stationary beds or a carousel system. Each setup for organizing and managing the casting and curing of precast elements has its own advantages and considerations.
Stationary Bed System
In a stationary bed system, precast concrete elements are cast and cured on fixed beds or platforms within the manufacturing facility.The production process involves casting concrete into molds placed on these stationary beds. After casting, the molds remain in a fixed position for curing and hardening. The mold generally must stay there for about a day until they get solid enough to remove the forms, lift them out of place, and take them off to put into the storage yard.
Carousel System
In a carousel system, precast concrete elements are cast on a rotating platform or carousel that moves through various stages of production.The carousel rotates to different workstations where casting, curing, and demolding processes occur sequentially. This allows for a continuous and efficient production flow as the carousel moves from one stage to the next.
Stationary bed systems usually require more floor space than carousel systems, which are designed for a more compact and continuous production flow. Stationary systems are more common in North America, while carousel systems are more popular in Europe, where space is often a bigger consideration.
What Is Next For Precast Concrete and Smart Production Facilities?
Precast concrete is gaining momentum due to its inherent advantages in speed and quality. As more businesses experience its superior quality and efficiency compared to on-site construction, we will see a transition toward prefabrication as a standard practice in the industry, likely increasing demand for smart factories as well.
The use of precast concrete has already expanded beyond traditional applications like residential and commercial buildings to include infrastructure projects such as bridges, tunnels, and even modular housing construction. In years to come, we will continue to see new applications for prefabrication in the industry.
The state of these technologies in the construction industry is dynamic, and ongoing developments in materials, techniques, and regulations will continue to shape the landscape. Two areas that can significantly impact the future include technological advancements and sustainability efforts.
Technological Advancements
As technologies such as BIM become more sophisticated, they enable precise planning, coordination, and execution, further improving project outcomes and emphasizing the need for a digital evolution from traditional building methods to advanced technologies. Currently exhibiting a spectrum of technological adoption, the precast sector can gain efficiency, productivity, and quality through the widespread use of advanced technologies and the rise of smart factories.
Sustainability Efforts
Sustainability has become a consideration for many projects in recent years as the industry works to reduce its environmental impact. Prefabrication and using precast concrete contribute to more environmentally friendly building practices and can help move the industry closer to its sustainability goals. Moving forward, we will see a growing emphasis on sustainable construction practices, including using precast concrete and developing smart factories.
Conclusion
The precast industry’s journey towards digitization and smart factories is paving the way for efficiency, reduced errors, and improved processes. Digital transformation, through automation, laser systems and comprehensive MES solutions, creates value for precast companies of all shapes and sizes by boosting their competitiveness and creating new possibilities never previously imagined.
Intelligent software solutions, like RIB One Prefab, provide integrated and digitalized production workflows for prefabrication. They enable automated management of the whole prefabrication production process, from sales and resource planning to production to logistics and mounting, taking the smart factory to a whole new level of efficiency. Book a demo to experience all these benefits today!

Most Recent
28 mins read
27 mins read
24 mins read
25 mins read
Blog Categories
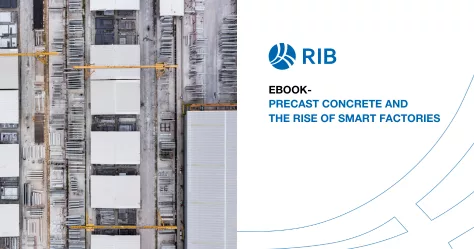
Ebook