28 mins read
Procurement Strategies in Construction: 9 Keys to Establishing Robust and Sustainable Procurement Processes
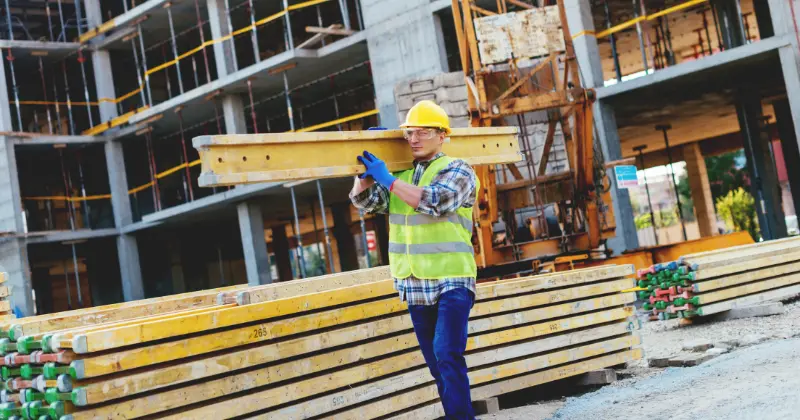
Procurement is an essential process in many industries since the goods and services needed to complete a project or meet customer demands must be available when needed to guarantee success. Procurement strategies in construction have evolved to improve supplier management practices while balancing cost savings and quality objectives.
In this blog post, we take a closer look at construction procurement strategies and their importance to the construction industry. We also review some tips and best practices for optimizing these strategies.
Types of Procurement Strategies in Construction
All projects require an effective procurement strategy to improve efficiency, reduce costs, and gain a competitive advantage. With the wide variation in project size and type, several different construction procurement strategies have emerged, each with inherent benefits and drawbacks.
- Traditional: Following this model, the client selects a general contractor who agrees to the financial terms laid out in the construction contract. Once work begins, the contractor takes responsibility for sourcing and material handling tasks. This method works well for small projects with minimal complexity.
- Design-bid-build: For larger projects with longer timelines, a bidding stage is added to the contractor selection process. The selected contractor will then pursue a procurement strategy that aligns with the elements laid out in their construction proposal and detailed bid.
- Design-build: This strategy involves selecting a single firm or contractor to perform both design and construction work. Since all project tasks are under the control of a single entity, this model can streamline procurement strategies that leverage existing supplier relationships and pricing agreements, especially for large and complex projects.
- Management contract: Some clients choose to hire a management contractor to assume responsibility for all aspects of construction work, including supplier and subcontractor management. This method is selected by clients seeking to outsource day-to-day decision-making and management to another responsible and trustworthy partner.
The choice of construction procurement methods and strategies impacts roles and responsibilities, collaboration methods, and project risks. The strategy selected must also provide adequate oversight to ensure procurement issues do not lead to delays or shortages.
What is the Importance of Effective Procurement Strategies in Construction?
A robust procurement strategy helps to control costs effectively while streamlining the flow of high-quality building materials and equipment throughout the project lifecycle. Avoiding budget issues is another key objective, with 98% of construction projects worldwide experiencing cost overruns. The important benefits of effective procurement strategies include:
- Cost savings achieved through favorable terms with suppliers
- Timely, well-planned deliveries to ensure materials are available while avoiding unnecessary stockpiles
- Reduced risk from supply chain disruptions, shortages, and material defects
- Improved quality through defined supplier and subcontractor selection processes
Effective procurement methods for construction projects also provide stability for complex projects struggling to meet aggressive timelines. As priorities, team members, and conditions change, reliable procurement and material handling practices ensure teams always have what they need to complete important activities.
What are the Challenges of Construction Procurement?
Successful projects can make the work of a construction procurement manager seem effortless since the tools and practices deployed to support these efforts are not always recognized until problems arise. In reality, developing effective strategies can be a difficult task in an industry where methods and expectations are continually evolving. Common challenges in construction procurement include:
- Budget constraints that preclude the purchase of high-quality building materials
- Diverse supply chains that require a mixture of supplier management strategies
- Project changes or logistical challenges and complexities impacting procurement
- Global or regional shortages that lead to excessive costs for essential construction materials such as lumber, steel, and drywall.
- Delayed cash flow due to external factors that impact the timeliness of payments
While many of these challenges cannot be avoided, effective procurement strategies in construction ensure the risks are minimized while supply chain flexibility is optimized. Careful planning, attention to detail, and advanced software tools streamline procurement processes to support favorable project outcomes.
Tips for Successful Procurement Strategies in Construction
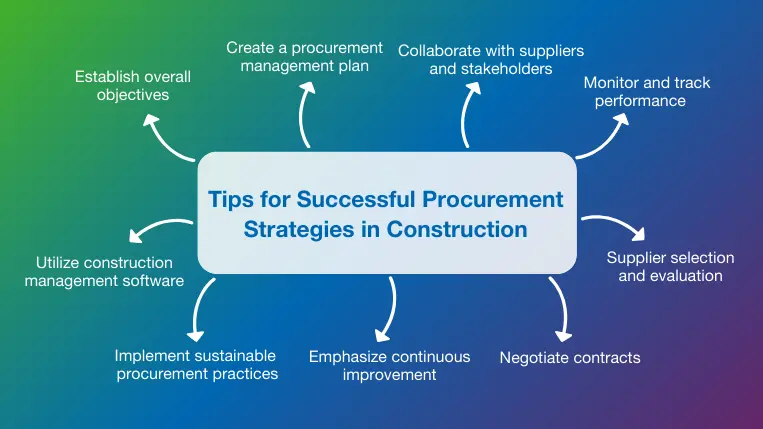
Selecting the right strategy is just the beginning. All types of procurement strategies in construction require a long-term commitment to remain consistent when priorities change, or inevitable surprises occur. Adhering to a few basic principles and best practices helps to optimize procurement outcomes throughout the project lifecycle.
1. Establish overall objectives
Procurement objectives should be established to align with the overall project goals and construction KPIs, such as operating cash flow, schedule performance index (SPI), and quality defect rates that are influenced by the procurement process. Well-defined objectives make it possible to assess the effectiveness of the procurement process throughout the project and make corrections as needed.
2. Create a procurement management plan
A procurement management plan can be created as a standalone document, or as an element of the overall project plan. In either case, the plan should define procurement roles and responsibilities, supplier management strategies, evaluation methods, and qualification practices. Quality standards for all materials, equipment, and services should also be included. The written plan should specify the budget and timeline for procurement activities to set appropriate spending boundaries and prevent overruns and delays.
3. Collaborate with suppliers and stakeholders
Transparent communication and ongoing collaboration provide benefits that span all aspects of the construction industry, but these practices are especially important in supporting effective procurement strategies. Collaboration with subcontractors, clients, and other construction roles helps keep quality issues, shortages, or delivery problems visible, while collaboration with suppliers allows problems to be resolved faster while avoiding misunderstandings and delays.
4. Monitor and track performance
Supplier performance monitoring should not be limited to reactive notices and warnings when suppliers underperform. Professional construction reporting systems support the generation of supplier scorecards, reports, and other ongoing performance monitoring tools to improve visibility. Communicating performance on deliveries, quality, change orders, and other important issues in a transparent and professional way helps to encourage cooperation and proactive responses.
5. Supplier selection and evaluation
Suppliers should not be selected based on price tag alone, and this is especially true of construction suppliers contending with seasonal demand, material and labor shortages, and increasing price pressure to remain competitive. A formal and unbiased supplier prequalification process includes a review of financial stability, experience, and technical capabilities that bring additional benefits to the project. These carefully vetted suppliers can then be leveraged for additional projects once the relationship is established.
6. Negotiate contracts
Negotiating contracts is essential since it allows project owners to obtain the best possible price, quality, and delivery commitments from highly qualified suppliers and contractors. Contract terms also formalize expectations for material cost control, payment schedules, and construction change management practices that must be defined before work begins. Complex projects with multiple stakeholders benefit from centralized construction contract management software that simplifies the review and sharing of detailed contractual obligations.
7. Emphasize continuous improvement
Perhaps the most important key to optimizing procurement strategies is converting the lessons learned from day-to-day challenges into ongoing improvements that can be carried from one project to the next. Supplier collaboration processes, delivery schedules, quality metrics, and cost reduction metrics always leave more room for future improvement, so capturing stakeholder ideas and benchmarking performance over time can strengthen procurement strategies.
8. Implement sustainable procurement practices
Sustainable procurement processes place additional emphasis on reduced waste, minimized embodied carbon, and environmentally friendly building materials for construction procurement methods. These practices can provide the benefit of short-term cost savings on materials while adding long-term value to the project through improved energy efficiency and regulatory compliance. A focus on social and environmental responsibility can also be an attractive attribute for prospective clients, suppliers, and building occupants.
9. Utilize professional construction management software
Procurement methods have grown more sophisticated over time, making it difficult to manage the resource requirements of complex projects using manual methods or spreadsheets. Construction procurement software helps in bid tendering, purchase order management, invoice reconciliation, and payment cycle. It also automates the management of materials, suppliers, and subcontractors, and ensures the right resources are available when you need them, at the best available price.
Conclusion
Procurement strategies in construction often remain in the background until costly and time-consuming material issues threaten the budget or schedule. Project managers, general contractors, and clients are now recognizing the value of procurement planning, supplier management, and sustainable practices to reduce supply chain risks. Software solutions also play a vital role in this transformation.
The integrated portfolio of RIB Software solutions streamlines procurement, scheduling, estimating, and other key project tasks by enhancing collaboration between stakeholders and providing the real-time data integration needed to meet project timelines and eliminate delays.
If you are ready to benefit from professional construction procurement software to manage orders, monitor material prices, and compare supplier bids, all in a centralized platform, get your free demo for RIB Software today!
Most Recent
28 mins read
27 mins read
24 mins read
25 mins read
Blog Categories

Ebook