24 mins read
Exploring the Top 10 Construction Trends for 2025

With 2025 looming around the corner, the construction sector is on the verge of a renaissance. Modular construction, 3D printing, and sustainable building methods aren’t just concepts for the future; they’re already changing how we design, build, and maintain structures.
We also know that with these exciting advancements come difficulties. Trends in the construction market, like labor shortages, continue to impact schedules and profitability, while supply chain disruptions and evolving economic environments are still forcing businesses to reconsider how they operate.
But it’s not all doom and gloom. Breakthroughs in construction software solutions, artificial intelligence, and robotics are opening up new possibilities, transforming every aspect of construction – from design to execution. For those who are willing to embrace innovation, these developments provide possibilities to succeed in an ever-competitive environment.
Keeping up with current building industry trends is now more important than ever. With that in mind, let’s look at the top 10 construction trends that will affect the sector in 2025 and beyond.
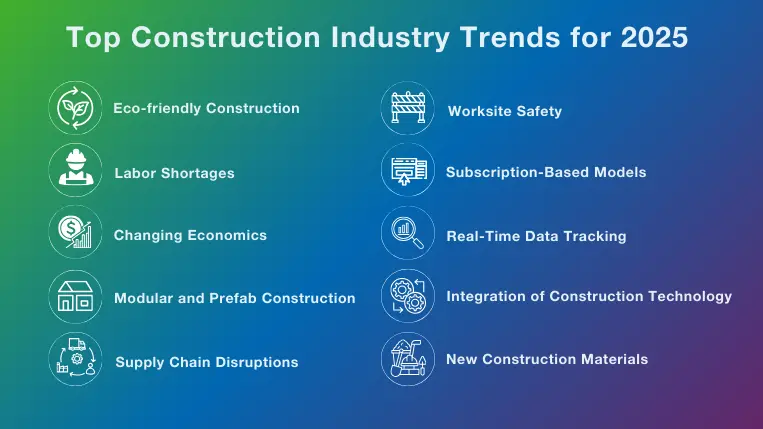
1. Eco-friendly Structures, Methods, and Tools
Sustainable construction is no longer a passing fad; it is the cornerstone of contemporary buildings, influencing project design, construction, and operation. The green building movement is gaining steam and offers significant environmental and economic benefits through the use of energy-efficient technology and ecologically friendly materials.
According to the 2024 Green Building Global Industry Report, the green building industry is predicted to reach $851 billion (€814 billion) by 2028, owing to rising public awareness of climate issues and environmental sustainability. The idea of green buildings is to minimize their immediate environmental impact while increasing the long-term efficiency of resources like water, power, and materials.
Embracing renewable energy options like solar panels, using recycled steel or bamboo, using sustainable construction software, and adding green roofs with energy-efficient green building designs are becoming more significant ways to reduce your environmental effects. One approach to differentiate yourself from the competition is to get green building certifications such as LEED (Leadership in Energy and Environmental Design). These certifications clearly demonstrate your commitment to sustainability and help you stand out in the business. They show clients that your organization cares about environmental responsibility, which can be a big selling point as the need for sustainable construction grows.
Sustainable equipment practices are further changing the construction industry. Important construction industry trends include switching to electric machinery, keeping equipment well-maintained for maximum efficiency, and using remanufactured components. (Interestingly, remanufacturing consumes just 20% of the energy required to produce new components, making it an ecologically friendly and cost-effective solution.)
According to a recent Fortune Business Insights report, renting machinery is expected to expand to $181.81 billion by 2031. This allows firms to reduce their carbon footprint and expenditure while accessing a wide range of equipment.
2. Labor Shortages: Finding Solutions Through Creativity and Planning
It’s no secret that the construction sector is dealing with a continuous labor shortage, which is creating delays, decreased productivity, and lower overall profitability. The workforce is aging, and there is an increasing need for qualified personnel. Trade occupations continue to endure unfavorable attitudes, resulting in an increasing skill gap.
In the United States alone, predictions are that by 2031, nearly 41% of the construction workforce will retire, while the sector will need over 500,000 extra workers to satisfy the present demand.
To effectively address these challenges, the industry should use a combination of innovative and traditional techniques. To begin, firms should concentrate their recruiting efforts on removing the stigma associated with trade occupations by highlighting the positives, such as competitive earnings and a speedier route to getting a job without the weight of school debt. Partnerships with high schools, universities, and trade programs may also help to develop a talent pipeline by engaging young adults early on and giving hands-on training.
Another critical step is to upskill the workforce via specialized training, mentorship, and professional development. Improving the skills of workers increases productivity, raises job satisfaction, and leads to employee retention. Mentorship programs enhance the flow of information among people, enabling experienced experts to share their skills and ideas with novices in the industry. Training programs that mix internal resources with external collaborations are also critical for equipping staff with the skills required to flourish in a changing business.
Finally, automation is increasingly seen as a vital answer to the challenges posed by the labor shortage. By streamlining repetitive tasks and improving workflows, digital construction technologies like autonomous machines and specialized robotics enable businesses to maintain production levels, even with fewer employees.
A big plus about automation is that it creates opportunities for younger, tech-savvy individuals who are attracted by the allure of these tools and systems to enter the industry. As autonomous technologies become more prevalent on job sites by 2025, teams under pressure will discover that they could be of valuable assistance.
3. Changing Economics/Market Dynamics
The construction sector will have to face significant challenges and opportunities in 2025, driven by evolving market factors such as increasing material prices, fluctuating interest rates, and supply chain disruptions. Firms must adjust quickly to handle these changes and capitalize on new opportunities.
Material price volatility caused by global demand and supply chain constraints continues to reduce profit margins and complicate project planning. The pricing of key components like steel, concrete, and timber remains uncertain. To address this, businesses are diversifying their sources, procuring locally, and looking for alternatives like recycled or modular materials.
Interest rate fluctuations also play a major role. Lower rates may promote new developments, while higher rates may stifle growth. Firms must actively monitor these construction market trends and make necessary adjustments to their project pipelines and strategies.
Evolving market needs are altering priorities, with increased interest in energy-efficient buildings, healthcare facilities, and data centers. Meanwhile, remote and hybrid work patterns could reduce demand for conventional office space.
Government financing for long-term infrastructure projects is another important consideration. Firms that adopt green practices and remain ahead of regulatory changes are better positioned to compete in this competitive market.
Understanding macroeconomic dynamics and using technology allows construction businesses to develop robust supply chains, sustain profitability, and fulfill the needs of a continuously changing sector. Being agile and forward-thinking will be critical for success in 2025.
4. Modular and prefabricated construction
Modular and prefabricated construction techniques are gaining traction because they effectively cut down on building time, expenses, and waste. These technologies improve quality control and efficiency by assembling construction components in a regulated setting, separate from the actual site. The modular construction industry worldwide is expected to see substantial growth, reaching $120.4 billion (€115 billion) by 2027.
The techniques employed in building are useful for tackling housing shortages and adhering to tight project timelines. Modular building has proven effective in rapidly constructing healthcare facilities in times of crisis, showcasing its flexibility and ability to scale. As technology continues to evolve, modular construction is poised to integrate digital design tools like Building Information Modeling (BIM), aiming to enhance efficiency and boost project results.
Moreover, modular building promotes sustainability by lessening disruptions at the construction site and cutting down on material waste. Being able to dismantle and transport modular units provides enhanced flexibility and adaptability, which aligns well with the changing demands of urban growth and using resources effectively.
5. Supply Chain Disruptions
In the past, the construction sector has faced major interruptions in its supply chain: The COVID-19 pandemic wreaked havoc on transportation, where shipments were rerouted to different ports or containers had to wait in ports for weeks; Russia’s ongoing conflict with Ukraine has affected the steel industry significantly, where steel prices have increased by a staggering 65%; and since November 2023, Yemen’s Houthi rebels launching missile attacks on commercial ships in the Red Sea have caused shipping costs to spike – sometimes doubling or even tripling.
Delays like these are major supply chain issues that result in material shortages and increasing expenses. The difficulties we’re facing will likely continue through 2025, necessitating decisive measures to lessen their effects. Companies are expanding their supply chains, investing in local manufacturing, and implementing just-in-time inventory strategies to enhance their resilience.
New technologies such as blockchain and the Internet of Things (IoT) are enhancing transparency and efficiency within supply chains. These options enable immediate monitoring of items, ensuring quick delivery and reducing the chances of delays. Companies are using predictive analytics to assess demand and improve inventory management, which helps reduce the impact of supply chain disruptions.
Working together with various parties, including suppliers, contractors, and customers, is essential for tackling challenges in the supply chain. Having open conversations and fostering teamwork can improve how we address challenges and handle resources, helping projects run seamlessly even when faced with outside difficulties.
6. Worksite Safety
Making sure construction site accidents are avoided is an essential responsibility, and new technology is improving how we handle these practices.
Devices that can be worn, like smart helmets and sensor-equipped vests, keep track of workers’ health and the surrounding environment, offering immediate alerts to prevent accidents.
Drones have also shown themselves to be quite useful for increasing workplace safety. They enable construction site managers to perform complete inspections of difficult-to-reach or high-risk places without putting workers in danger. Drones can test structural integrity, track progress, and even detect safety hazards from the air, giving critical information for quick decision-making.
Automation and robotics also improve safety by taking on risky or repetitive jobs. Robots, for example, can handle demolition or heavy lifting, limiting human exposure to potentially dangerous conditions.
These developments, paired with a strong safety culture, allow businesses to protect their employees while maintaining productivity. Construction businesses can create a safer, more secure work environment for all employees by investing in these safety technologies and training programs.
7. Subscription-Based Models for Accessing Technology
As the industry approaches 2025, the adoption of subscription-based models is likely to increase significantly. According to a McKinsey & Company report, the architectural, engineering, and construction (AEC) industry, which has historically been sluggish to digitize, is now fast adopting digital solutions owing to increasing infrastructure demand and skilled labor scarcity. This trend is accelerating the use of subscription-based software services, which provide scalable and cost-effective project management and collaboration solutions.
In addition, the Royal Institution of Chartered Surveyors (RICS) “Digitalization in Construction Report 2024” cites a consistent increase in the industry’s usage of digital technologies. This trend suggests an increased dependence on subscription-based digital platforms to improve construction project efficiency and sustainability.
Providers are expected to broaden their offers to include packaged solutions, which include software, hardware, and training in a single, complete package. This method not only streamlines procurement but also assists businesses in developing unified, technologically enabled workflows.
Subscription-based models like RIB CostX or RIB Candy provide businesses with a cost-effective, scalable option to implement cutting-edge solutions without the large initial investment often needed for software and equipment. From design and project management platforms to innovative construction machinery, subscriptions make it simpler than ever for businesses of all sizes to remain competitive in the industry.
Subscription-based models make capabilities previously only available to major organizations more accessible to the average-sized construction company. Small and medium-sized businesses can now afford technology like drones, robots, and augmented reality (AR) systems which are being employed for site inspections, progress tracking, and virtual walkthroughs. Subscriptions also include IoT devices that offer real-time data on equipment operation, material use, and worker safety.
One of the primary benefits of subscription-based models is their inherent scalability. Companies only pay for what they use, whether it’s a monthly project management software subscription or job-specific rental of machinery. This flexibility is especially useful during times of economic uncertainty, enabling businesses to better control costs while preserving access to critical tools.
Many subscription systems are cloud-based, allowing for seamless communication across teams and stakeholders. This is especially useful in construction, where real-time communication and updates are essential for keeping projects on schedule.
Companies can promote better transparency and collaboration in construction projects by subscribing to systems that combine scheduling, budgeting, and design processes, resulting in more effective project delivery.
8. Real-Time Data Tracking
Real-time data-driven decision-making is transforming building operations, improving efficiency, safety, and cost management. For example, IoT sensors built into equipment and materials monitor temperature, humidity, and performance. These insights enable project managers to address potential issues before they worsen, thus decreasing downtime. Meanwhile, digital twins provide real-time virtual representations of construction sites or structures. These models use IoT data to provide unique insights into the state and performance of projects.
Wearable technologies, such as smart helmets and vests, can track workers’ health, tiredness, and environmental risks. This immediate information helps to create safer and more successful workplaces.
Furthermore, predictive analytics (information gathered during the construction process) estimates the building’s maintenance requirements after it is completed. Property owners and facility managers can plan for maintenance to prolong the life of their assets and save on operational costs.
Finally, construction analytics software, like RIB BI+, is transforming project management by delivering real-time performance monitoring and useful data. This technology enables project managers to monitor important metrics like productivity, cost, and resource allocation in real-time, allowing them to address inefficiencies and risks proactively. With intuitive dashboards and data visualization capabilities, these systems provide a full perspective of project health, allowing teams to work efficiently and remain on track.
9. Integration of Construction Technology
The way we make decisions in building operations is changing thanks to real-time data. This shift is leading to better efficiency, improved safety, and smarter cost management. Sensors connected to devices and materials keep track of temperature, humidity, and overall performance. These insights help project managers address potential problems early on, minimizing downtime.
Devices that can be worn, like smart helmets and vests, can track the health, fatigue levels, and environmental hazards faced by workers. This timely information helps in creating safer and more efficient work environments.
By 2025, many construction companies will have started to integrate other modern technology into every part of their operations, including:
Building Information Modeling (BIM). BIM promotes effective collaboration among architects, engineers, and contractors within the construction sector. For the year ahead, we can anticipate smoother integration of BIM with AR and VR technologies, improving the overall experience of project walkthroughs. BIM management software also continues to play an important role, recognizing potential issues across disciplines early on and helping to eliminate expensive errors and holdups.
Drones and Robotics. Employing drones and robotics can significantly reduce the time and expenses associated with site surveys, monitoring progress, and performing inspections. Meanwhile, machines take care of repetitive jobs like laying bricks and pouring concrete, enhancing accuracy and minimizing errors that people might make.
AI and Machine Learning. Contractors can leverage AI and Machine Learning to better predict project costs, manage delays, and enhance resource allocation. Machine learning algorithms analyze project data to uncover trends in construction, which enhances decision-making over time.
5G Networks. By 2025, 5G networks will improve IoT connectivity, allowing for smooth interactions among devices, employees, and management systems.
10. Development of New Construction Materials
By 2025, the drive for materials that are efficient, durable, and environmentally friendly will spark new innovations. According to StartUs Insights, by 2025, startups are developing advanced materials such as biodegradable plastics, thermally adaptive fabrics, and flexible displays, which offer improved physical properties and sustainability.
Here’s a look at some of the construction materials that are making headway:
- Materials Developed through 3D Printing. The application of 3D printing in construction has enabled the creation of customized materials for particular purposes. These are specialized concrete mixtures designed for quick application and long-lasting performance in printing applications.
- Microbial Concrete. Employing microbial concrete to repair cracks lowers maintenance expenses and enhances the durability of structures.
- Transparent Aluminum. Transparent aluminum represents an innovative material that combines the durability of steel with the clarity of glass, making it perfect for stunning architectural designs.
- Phase-Change Materials (PCMs). PCMs are used in construction to help control indoor temperatures by absorbing and releasing heat. This concept enhances energy efficiency independently of HVAC systems.
- Hempcrete. Hempcrete is a lightweight, sustainable material made from the hemp plant. It offers excellent insulation, moisture regulation, and carbon-sequestration properties, making it one of the best sustainable construction materials and an eco-friendly alternative to traditional concrete.
Final Thoughts
The future of the construction industry is exciting because the progress we’re witnessing, including sustainable practices, subscription-based technology, innovative materials, and real-time data monitoring, is transforming our construction processes. Staying informed about the newest construction industry trends and applying them will be crucial for success in our changing world, and embracing these innovations will allow us to address the needs of modern society while paving the way for a more sustainable and connected future.
RIB Software offers a cutting-edge suite of solutions tailored to enhance quality, foster collaboration, and ensure the timely completion of construction projects. If you are ready to explore the potential of innovative construction technology, get your free demo today and see how RIB can elevate your business to new heights!
Most Recent
24 mins read
25 mins read
24 mins read
21 mins read
Blog Categories
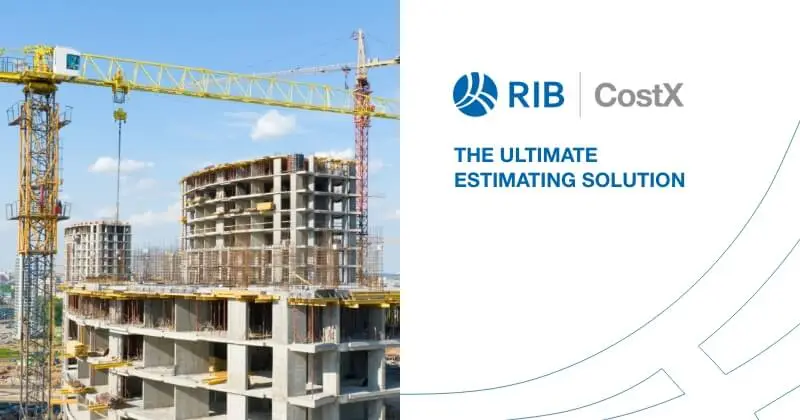
Ebook