28 mins read
Exploring Specification Management Best Practices, Challenges, and Definitions

Accurate and timely documentation is essential in any industry, especially when the pace of change makes it difficult or impossible to manage files effectively without the use of digital tools. Specifications management benefits organizations in many ways as they safeguard their quality and compliance in the face of challenging schedules and budget constraints.
In this blog, we’ll discuss the definition and advantages of specification management, along with some common challenges that can potentially undermine the benefits in any industry. We’ll also review some important tips and best practices that help organizations optimize the process as they integrate new software tools and practices.
What Is Specification Management?
Specification management is a systemic process for creating, updating, and maintaining documents throughout the lifecycle of a project or product. These specs include drawings, contract documents, and information sharing and tracking procedures.
In the manufacturing industry, spec management is the key to establishing and maintaining consistent production line operations, supply chains, and design controls. As products, processes, and procedures evolve, an effective system creates a centralized source of truth to keep all stakeholders on the same page. This same value applies to businesses ranging from restaurants and retail outlets to pharmacies and software development firms.
Specification Management in Construction
Building companies and their clients use construction specifications to establish and document mutual expectations for the scope of work, quality requirements, installation methods, and many other aspects of the project. The specification management process ensures these documents remain current, accurate, and easily searchable for dispersed teams and stakeholders.
What are the Benefits of Efficient Specification Management?

Specification systems and the software used to create and maintain them deliver many advantages to businesses of all types. By optimizing the accuracy and availability of key business documents, the specification management process improves both quality and efficiency.
Centralization
Specification control involves coordinating important documents in a centralized database where everyone can simultaneously access the most current information. Centralization is especially important when complex products and projects are continually changing. Digitized spec management platforms are the key to effectively controlling and organizing thousands of dynamic files while eliminating cumbersome paper filing and approval systems.
Reduced errors
When siloed teams or individual workers refer to outdated or inconsistent information, nonconformances, rework, and costly delays can result. Centralized, accessible specs reduce the risk of defects and errors by minimizing the chance of miscommunication or inconsistencies between released copies.
Streamlined procurement
Purchasing processes rely on accurate part specifications, cost data, and lead time information to avoid hiccups during the ordering, receiving, and inspection steps. Spec management is the key to maintaining accurate component information that can be integrated with Enterprise Resource Planning (ERP), cost estimation, and Computer-Aided Design (CAD) software platforms.
Traceability and compliance
Version control enhances traceability since historical records indicate who changed specs, what was changed, and when. The specification management process also produces an audit trail that allows discrepancies or compliance questions to be investigated with less time and effort.
What are Common Challenges in Specification Management?

Despite the obvious benefits and efficiencies, specifications management is not without limitations and challenges requiring ongoing attention.
Having a common language across specs
Specification management involves more than just collecting documents, drawings, and records in a digitized database. Standardized formats, terminology, and naming conventions ensure specifications are interpreted consistently, making integration with other software platforms possible. Ensuring adequate levels of standardization requires ongoing attention. Specification management software helps businesses identify defects and weaknesses that lessen the integrity of the database.
Incomplete information
Effective spec management also requires a complete data set for each part, project, or process. For example, a construction drawing set might include elevation, sectional, or detail drawings to supplement higher-level structural drawings and floor plans. Related specifications must remain organized and synchronized when changes occur, or document life cycles change. Verifying complete information requires a combination of effective software tools and sound specification management practices.
Outdated information
The availability of accurate and up-to-date specs distinguishes the best specification management processes from the siloed, paper-based methods that once prevailed. Real-time updates and revision control processes help to segregate obsolete content while keeping them available for audits or historical review. Access management features ensure only system administrators and other select individuals can move or rename files.
Remote and mobile access
Centralized specification management and change control systems are valuable for stakeholders in the workplace and the field, especially in industries like construction, agriculture, and renewable energy, with boundaries extending far beyond the office. Cloud-based, mobile software platforms prevent delays in information transfer and change implementation for contractors, estimators, and other decision-makers in remote locations.
Top 5 Specification Management Tips & Best Practices

Spec management practices impact the efficiency, quality, brand reputation, and bottom line of millions of small and large businesses worldwide. Getting the most out of these systems requires careful planning, tool selection, training, and follow-up.
1. Establish clear standards
The first step towards effective spec writing and management is the establishment of standards to guide document creation, content writing, and approval processes. Clear and consistent standards allow stakeholders to review specifications efficiently while ensuring compliance with external regulations and industry norms. Establishing these baseline formats, templates, and content requirements also helps to:
- Ensure the essential information required for each specification type is included
- Accelerate the training process for new specifications or changes
- Scale the organization as the number of documents and records multiplies
- Create documents faster without developing formats from scratch
2. Decide on system capabilities
Not all spec management systems are created equally, so you need to discover what features are necessary for your organization’s size, type, and scope and what will help you align with industry standards. For example, American medical device manufacturers must establish FDA-compliant supplier and process documentation control systems. At the same time, construction companies must stay current with standards, including ISO 19650 for Building Information Modeling, LEED standards for sustainable buildings, and (in the UK) Construction Design and Management regulations.
Each option has capacity limitations, data security features, and reporting capabilities tailored to specific industries or designed as a one-size-fits-all with more generic workflows. Customization and scalability are additional considerations impacting the long-term fit of the specification management system.
3. Use professional specifications management software
Advanced software tools support consistent digital formatting, real-time updates, and unabridged traceability that make specification control so valuable. Spec management software creates a reliable information hub to facilitate real-time collaboration between office and field employees and ensure projects run more smoothly.
RIB SpecLink is a cloud-based, centralized specification platform with automated workflows, smart linking technology, and mobile or web-based access to accommodate the complexity and diverse conditions of construction and other industries.
4. Benefit from Office Masters
Extending on the point above about using professional software like RIB SpecLink, another best practice for successful specifications management is to benefit from powerful features like Office Masters. Office Masters are templates architectural and construction firms use to standardize the specification process across projects instead of creating a different spec manual for each project. A well-maintained Office Master saves firms time in creating specs from scratch, and it reduces the risk of errors and costly rework, as the different trades can access a single, online version of specs, eliminating version control issues and potential misunderstandings.
The topic of Office Masters was recently discussed in an insightful episode of our webinar series RIB SpecTalk. You can check out the episode for more insights about this powerful feature from SpecLink below:
5. Conduct ongoing employee training
No specification management process or tool can be effective without comprehensive employee training to ensure everyone understands where to find the specs and templates needed, how various document types and systems interrelate, and why revision control is essential for maintaining quality and compliance.
Training also allows employees to better understand their unique role in keeping the database accurate and complete while minimizing the risk of breaches and other data security issues. The specification system itself becomes a useful training tool when new revisions are automatically pushed out for read and understand (R&A) training, and employee training records are easily accessible for managers and human resource teams.
6. Complete regular updates
The specification management process is a bit like a garden where new plants and flowers arrive by the day, accompanied by a few weeds and overgrown hedges requiring expedient maintenance. In either situation, continuous review, adjustment, and problem resolution are recommended best practices. Regular system updates and maintenance should include the following:
- Compliance checks to ensure specifications meet the latest industry regulations.
- Technical reviews to ensure documents are accurate and complete.
- Review of spec creation, storage, and change practices to identify opportunities for improvement.
- Updating specification software with the latest features and security patches.
- A review of access controls to verify that only authorized users can view or modify files.
Conclusion
The importance of spec management comes into sharp focus in industries where document accuracy and availability can spell the difference between success and failure. Software tools to streamline these key processes have allowed businesses to scale operations to unprecedented heights without compromising their commitments to quality and efficiency.
RIB SpecLink, our professional specs software, has decades of experience streamlining the specification management process, offering a smart and innovative platform to manage all documentation, reducing the risk of errors and omissions, and increasing productivity and collaboration.
If you are ready to streamline your specification workflows with state-of-the-art technology, get your free demo for RIB SpecLink today!

Most Recent
28 mins read
27 mins read
24 mins read
25 mins read
Blog Categories
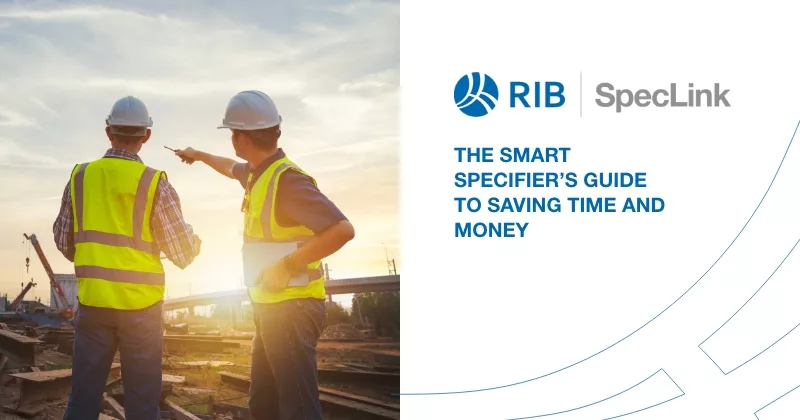
Ebook