28 mins read
First Principles Estimating: What Do I Need to Get the Job Done?
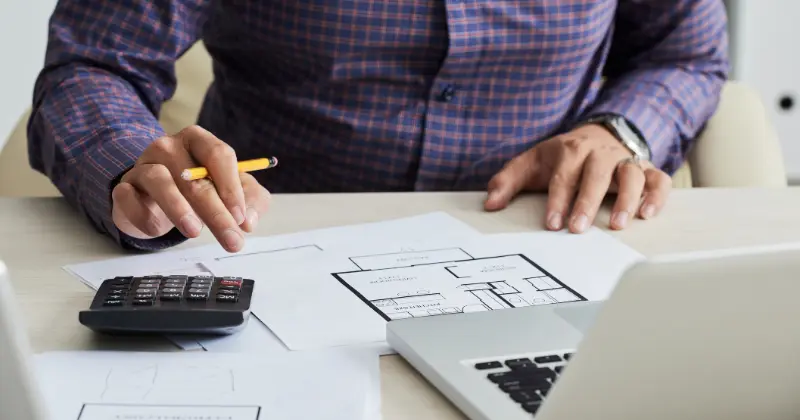
Accurate construction cost estimation is one of the most important aspects of a project’s success. It helps allocate resources effectively and plan for a budget to ensure the expected quality and profitability levels.
There are many methods and types of estimates in construction projects. Today, we are examining one of the most important ones: first principles estimating. This invaluable method, also known as “bottom-up estimating,” breaks down the project into smaller components to make it easier to analyze and estimate the resources necessary to complete each component. It is the most accurate method and one that is preferred by companies today.
Keep reading to learn everything about it!
What is First Principles Estimating?
First Principles Estimating is the process whereby an estimator identifies, considers, and collates the estimated individual costs, quantities, and production of every resource needed to complete individual items of work or tasks and, ultimately, a project successfully.
RICS defines the methodology in their “Cost Prediction Professional Standard” as the “method of preparing a cost estimate by calculating the monetary rate, labor hours, and rates of productivity required to complete each of the individual tasks within the desired breakdown structure.”
In doing so, they not only determine an accurate expected total cost of all the resources needed but also gain a thorough understanding of the requirements, in terms of quantity and outputs, for a build that can be managed and controlled throughout the project’s lifecycle.
These resources, which typically fall into the categories of material, labor, plant, subcontractors, and overheads, range from simple to varying levels of complexity. For example, sand, stone, and cement are simple resources that can be purchased. Combined in their respective proportions, they form what is known as a complex or combination resource, i.e., concrete materials mix. Adding the hiring cost for a dumper and the labor required to operate it and to mix and place concrete attains yet another level of complexity. Rest assured, the resources may become more complex, but the pricing becomes simpler!
In summary, First Principles Estimation answers the question, “What do I need to get the job done, and how much will it cost?”
The Benefits of First Principles Estimating
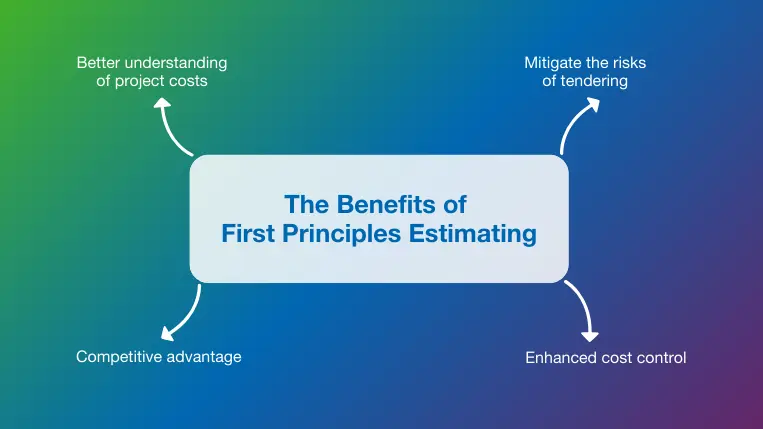
By embracing First Principles Estimating, construction companies can accurately forecast a project’s cost, resource quantities, and target production and, in doing so, anticipate, mitigate, and proactively troubleshoot or model problems and changes if, and when, they occur.
- Better understanding of project costs: One of the first benefits of using this estimating method over others is that it provides a better understanding of the project’s actual costs and other requirements. This is due to the detailed analysis of all project elements required to complete the estimate, which translates into a higher degree of accuracy and better strategic decisions.
- Mitigate the risks of tendering: Accurate estimating is fundamental during a tendering process, especially for lump sum projects. This estimation method eliminates the risks of pricing the project incorrectly, as every type of resource required is carefully calculated and analyzed to arrive at a fair price.
- Cost control: The detailed structure generated using first principle estimating facilitates cost control in construction projects, allowing companies to easily compare actual costs against budgeted ones to ensure everything is going as expected and profit is not affected.
- Competitive advantage: Last but not least, first principles pricing provides contractors with a significant competitive advantage by allowing accurate estimates that consider contingencies and all other factors when pricing the project. This puts them in a position to bid for bigger projects that other competitors might skip.
How to do a First Principles Estimating
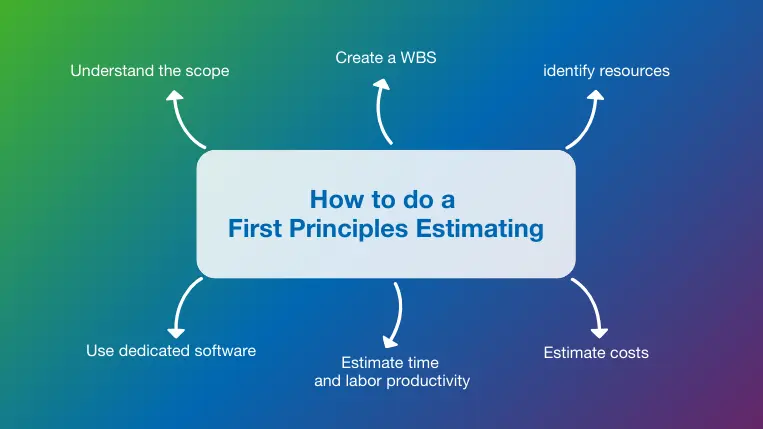
Understanding how to carry out this estimating method is fundamental to success. Below is a breakdown of the steps to be followed and some tips and best practices to ensure success!
- Understand the scope: The first step in the process is to carefully understand the project’s scope and requirements, as this will significantly influence estimates. While other estimating methods rely solely on historical data to price the project, first principles analysis ensures the estimation considers all specific elements of the project. Therefore, understanding site conditions and other important aspects of the project is fundamental at this stage.
- Create a WBS: As mentioned earlier, this method of estimating is completed by dividing the project into smaller components. To do so, you must generate a detailed work breakdown structure (WBS) that lists all the items of work to be completed. This breakdown will help you estimate the labor, materials, equipment, and other resources needed to complete each component. Examples of components include excavation, foundation work, plumbing, finishing, etc.
- Identify resources: Once you have broken down the project into smaller components, you can start investigating each component and identifying its indirect and direct costs. Direct costs are materials, labor, and equipment, while indirect costs can be utilities or other administrative costs.
- Estimate costs: The next step is to determine the costs of the identified resources. For this, you can reference historical cost data for similar projects, vendor quotes, and other sources of information. Considering construction contingencies in the estimating process is of the utmost importance as they will avoid losing profit over unexpected issues.
- Estimate time and labor productivity: In addition to estimating the costs of materials and equipment, you must also calculate the duration of each component and the labor productivity rates to truly get an accurate estimation of its price.
- Use dedicated software: This is more of a best practice rather than a step. Calculating all the resources that go into completing an item of work is not easy. Therefore, companies should move from manual spreadsheets and use specialized construction estimating software to manage the task. For instance, RIB Candy allows users to price using first principles estimating to improve estimates’ speed, accuracy, transparency, and audibility.
Final Thoughts
As you learned throughout this post, first principles estimating is a great method for getting a granular view of the project’s resource requirements, ensuring more accurate budgeting than other methods. However, this level of accuracy does not come free. The method can be very time-consuming if not handled with the help of professional estimating software like RIB Candy.
Designed to incorporate First Principles Estimation at its core, RIB Candy allows estimators to price and tender precisely using resource-based principles, free-format rate sheets, and a range of cutting-edge features. Whether it’s pricing items manually or via import from Excel, applying predefined formulas, analyzing resource usage and wastage in real time, or re-purposing project data from a previous project for use in a new one, RIB Candy takes project tendering and cost estimation to a whole new level. If you want to experience the power of RIB Candy, get your free demo today!
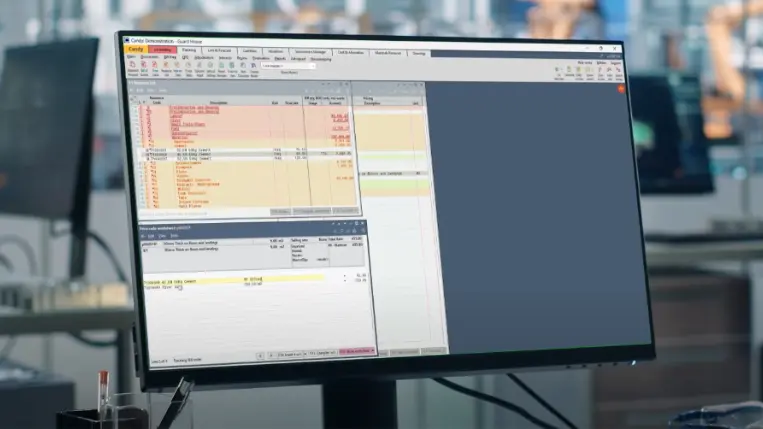
Most Recent
28 mins read
27 mins read
24 mins read
25 mins read
Blog Categories
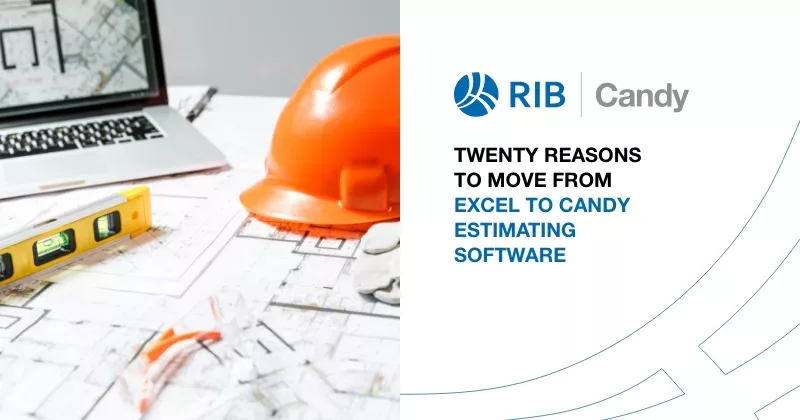
Ebook