24 mins read
Construction Quality Management: Reviewing the Benefits, Challenges, and Best Practices
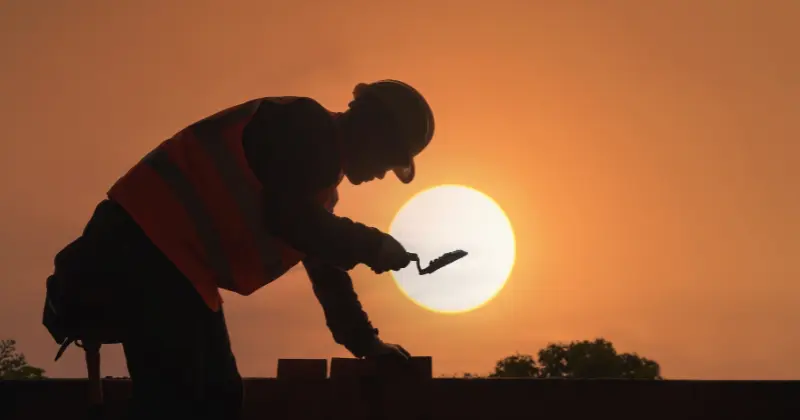
Construction quality can be defined and measured in many ways, including adherence to drawings and specifications, or minimized rework and errors. While all quality metrics and standards can add value to projects, the real benefits of quality come from satisfied customers and repeat business. Effective construction quality management practices provide the best possible outcomes by focusing on the most important goals and objectives.
In this blog post, we review quality management in construction and take a closer look at the responsibilities, benefits, and common issues. We also provide a list of helpful tips to ensure quality management plans are useful and relevant.
What is Construction Quality Management?
Construction quality management is the set of processes and practices used to maintain quality standards and expectations for construction projects. This means ensuring all work adheres to specifications, standards, and client requirements throughout the project lifecycle.
Comprehensive quality management practices also reduce waste and improve efficiency by ensuring activities are done right the first time. Quality planning activities are necessary to identify appropriate requirements and methods. Quality control (QC) practices like audits, inspections, and tests verify construction standards are being met through firsthand evidence.
Quality assurance (QA) activities are more preventive in nature, and include things like training programs, written procedures for quality control teams to follow, and the analysis of data to prevent future issues. Construction project quality management practices bring all of these facets and activities together under a common umbrella to create a culture of continuous improvement.
To learn more about these two processes, check our blog about quality assurance vs quality control in construction.
Who is responsible for quality management in construction?
Everyone who participates in a project must play a part in upholding high-quality standards, but the construction project manager is often given primary oversight responsibility for the construction quality management system. Contractors and subcontractors are also expected to participate in day-to-day quality monitoring and reporting activities, while project owners set the overall quality expectations.
Larger projects might have dedicated quality assurance teams assigned to manage quality documentation and perform regular inspections and site audits. When a HSEQ manager is retained to implement health and safety policies across multiple projects, their responsibilities often include regulatory compliance and quality management tasks, such as establishing new quality standards and keeping stakeholders informed on the latest quality and regulatory requirements.
Construction Quality Management Benefits
The benefits of construction quality are obvious, with materials and workmanship that conform to expectations contributing to schedule adherence and satisfied customers. Despite this recognition, rework due to inadequate controls, poor material quality, incorrect work instructions, and other avoidable issues are still commonplace on construction sites. Strong quality management practices help to minimize or prevent these problems by:
- Identifying issues before they lead to major problems and mitigating risks
- Maintaining regulatory compliance to avoid legal challenges and delays
- Enhancing project safety through hazard identification and training
Minimized rework and waste, improved efficiency and safety, and effective data quality management all lead directly to reduced project costs and optimized profitability.
Common Quality Management Issues in Construction
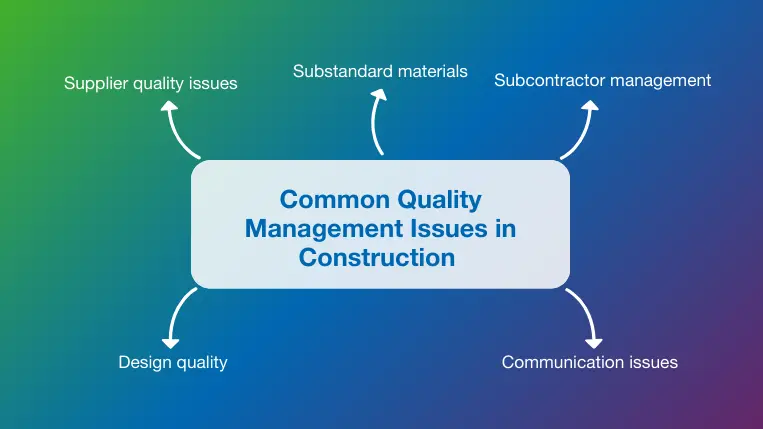
Complex construction projects bring people, equipment, materials, and sites together in new and unique ways for each individual project. This complexity makes careers in construction satisfying, but it can also become the source of quality issues.
Supplier quality issues
The wide variety of suppliers and commodities needed to make a construction project successful calls for a structured approach to supplier quality. Vendor qualification practices, regular audits, and on-site material inspections prior to shipment are practices that prevent supplier quality problems and missed deliveries from derailing project schedules. Dual sourcing is another effective supplier quality strategy, although 66% of construction supply chain leaders struggle with finding suitable alternate sources.
Substandard materials
Material issues can result from inadequate supplier quality practices, but there are many other material problems that impact project quality. Commodities such as lumber, insulation, and sheet rock can be damaged by moisture or improper storage. Inadequate material testing can cause quality issues in materials like concrete, steel, and asphalt to be missed, potentially leading to serious design or safety flaws. The importance of material quality makes it a primary focus area for quality management in construction projects.
Subcontractor management
Carefully selecting subcontractors and monitoring their progress throughout the project lifespan is an essential quality assurance task, since human error is a leading cause of quality issues. Subcontractors should always be thoroughly vetted, trained on appropriate quality and safety standards, and closely monitored so that workmanship issues and errors can be corrected quickly.
Communication issues
Contractor errors, supplier quality problems, and material issues can often be traced back to poor communication in construction projects. One of the primary objectives of quality management is establishing effective communication and collaboration channels to minimize misunderstandings and ensure important changes and alerts are not missed or delayed. Transparent communication practices also enhance quality through improved teamwork and problem-solving.
Design quality
The quality management process begins long before the first shovel of dirt is moved. A poor design or incomplete construction specifications can become the source of many quality issues that are difficult to mitigate. For example, improper structural analysis during the design phase might lead to complications during construction that require unplanned and expensive redesign and rework to correct, affecting the project’s profitability.
Best Practices for a Successful Construction Quality Management Plan
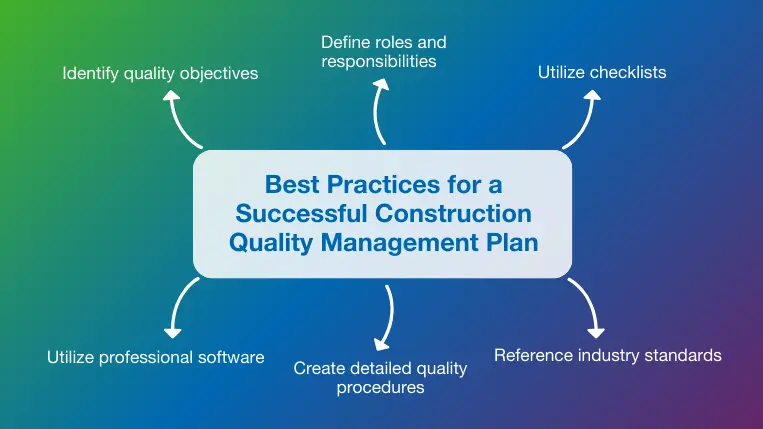
A construction quality management plan outlines the important procedures, processes, and standards a project will follow to optimize quality and meet predefined goals. Following a few basic best practices can ensure the process is successful.
1. Identify quality objectives
The most important function of the quality plan is capturing high-level quality objectives and expectations for the project. This includes monitoring construction KPIs with clear goals and targets for rework costs, safety incident rates, training compliance, and other quality-related metrics. All objectives in the plan should meet the SMART (Specific, Measurable, Achievable, Relevant, Time-bound) criteria and align with overall project goals.
2. Define roles and responsibilities
Confusion over quality roles and responsibilities can be a serious problem in construction, since the activities often overlap between contractors, subcontractors, and other team members. The construction quality management plan provides the first and best opportunity to clearly define responsibilities by role, project phase, and individual. Since these responsibilities are likely to change throughout the course of the project, this section of the plan must be reviewed and updated often. Setting clear roles can also help solve issues quickly as the person in charge is clearly defined.
3. Utilize checklists
Traditional checklists are still valuable for construction quality management when they are used to detail material inspection criteria, list audit questions, or document safety inspections. Checklists within or outside of the quality plan ensure no important quality features and requirements are missed, while providing easy-to-review records of deliverables being completed. Construction software solutions make it possible to complete quality checklists electronically, using mobile devices or tablets.
4. Reference industry standards
Along with the quality standards and expectations set forth by project owners and clients, it is important to list all external quality standards that the project must follow. Depending on the geography and project type, these standards might include:
- Local building codes and regulations
- Environmental standards dictating land and water usage
- Industry-specific workmanship and test standards
- Worker safety standards such as OSHA (US) or the Health and Safety Executive (UK)
5. Create detailed quality procedures
The construction quality plan should be a high-level document that sets the tone for project quality. Not all guidance and instruction can be captured in this plan, so individual procedures for testing, monitoring, supplier controls, auditing, and other essential quality areas should be created and referenced. Each of these procedures should be revision-controlled and updated when new quality practices are introduced.
6. Utilize professional software
The tips above are incredibly valuable practices to successfully manage quality in construction. However, the most important best practice for success is investing in software solutions like RIB Connex to help streamline essential quality functions. Our powerful solution offers robust quality management features allowing you to digitize quality processes faster and more collaboratively. A powerful defect management tool ensures teams can perform on-site inspections and assign tasks directly to subcontractors for effective and agile defect resolution. Likewise, the design collaboration module identifies constructability issues early, helping teams coordinate design and manage collisions to avoid extra costs and ensure quality.
Conclusion
Effective quality systems require the cooperation of everyone involved, and construction quality management practices combine objectives, tools, and practices to create a more unified quality culture. RIB Connex is an ideal platform for team communication and collaboration, with insightful dashboards and standardized workflows that provide instant access to quality plans, checklists, procedures, and inspection results.
RIB Connex empowers businesses worldwide to unlock the power of data and weave a digital thread through their most essential quality tasks, all with collaboration at the forefront. If you want to experience the power of digital quality management, get your free demo for RIB Connex today!
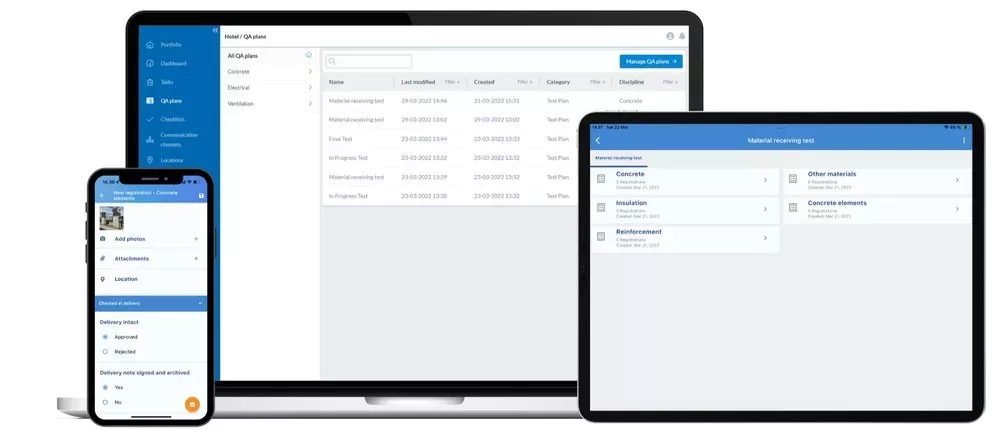
Most Recent
24 mins read
25 mins read
24 mins read
21 mins read
Blog Categories

Ebook