16 mins read
Decarbonizing Construction: The What, Why, And How
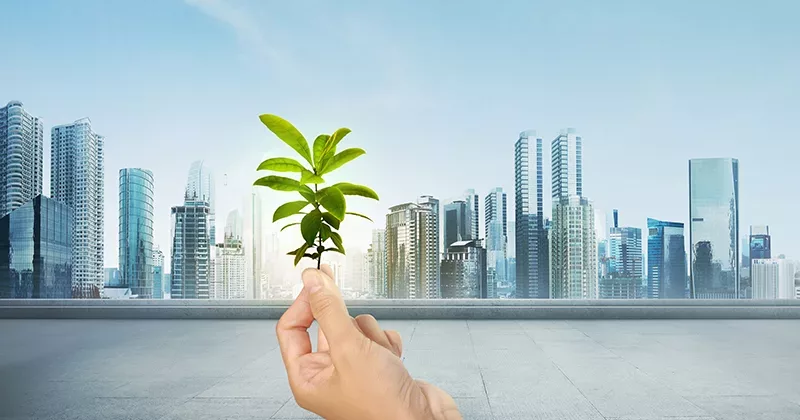
- What Is Decarbonization?
- What is Decarbonization in Construction?
- Understanding the Need for Decarbonization in The Construction Industry
- Benefits of Decarbonizing Construction
- Embodied Carbon Stages in Construction: Life Cycle Assessment
- How Can Construction Decarbonization Be Accelerated?
- Best Practices to Embed Sustainability into Your Construction Projects
- Moving Towards a Net Zero Future
Every year, when we celebrate Earth Overshoot Day, the ecological overrun becomes more and more obvious. According to the Global Footprint Network, this is a watershed moment since it marks the year when the Earth’s natural resource consumption will surpass its regeneration potential. Earth Overshoot Day is a stark reminder of the critical importance of decarbonization and climate action.
The Global Footprint Network announces the date for Earth Overshoot Day of the running year on June 5, which is also World Environment Day. Earth Overshoot Day 2025 fell on July 24th, 7 days earlier than last year on August 1st.
Rising sea levels, melting polar ice caps, destructive wildfires, and other extreme weather occurrences are all signs of the present climate crisis. Consider the devastating wildfires that swept through Australia in 2019 and 2020, causing widespread devastation and grief. These wildfires were exacerbated by global warming, the endangerment of species, and the degradation of ecosystems.
In light of these catastrophic dangers, the need for decarbonization is growing rapidly. Its primary goal is to decrease emissions of carbon dioxide and other greenhouse gases by increasing energy efficiency and shifting from fossil fuels to renewable energy. The importance of decarbonization is being recognized by an increasing number of countries, and these nations are setting ambitious goals to achieve carbon neutrality. But what does decarbonization truly mean?
In this blog, we will discuss decarbonization in the construction industry, including its necessity, methods for measuring embodied carbon, and strategies companies can implement to reduce their carbon footprint in construction.
What Is Decarbonization?
As its name suggests, decarbonization refers to the reduction of carbon; it involves phasing out man-made carbon dioxide (CO2) emissions into the atmosphere, with the ultimate goal of eliminating them.
The 2015 Paris Agreement set out an ambitious goal: to limit global warming to well below 2 degrees Celsius, and preferably to 1.5 degrees compared to pre-industrial levels, the threshold below which the Earth must stay to avoid the worst climate impact according to the IPCC’s report. It also finds that global net human-caused emissions of carbon dioxide would need to fall by about 45% from 2010 levels by 2030, reaching ‘net zero’ around 2050.
What is Decarbonization in Construction?
Decarbonization in the construction industry encompasses all efforts to reduce carbon emissions resulting from the processes involved in building and maintaining structures within the built environment.
Decarbonization in the construction industry involves reducing carbon emissions related to the production, use, and disposal of anything that goes into a building. That covers everything from building materials to construction techniques to the operation of the finished structure. Switching from carbon-heavy supply chains, as when the industry uses mixes of concrete and adhesives to secure many types of structures, is one way to reduce emissions. A 2019 conference presentation by Thornton Tomasetti, an engineering firm, cited potentially 12 percent less carbon being emitted by using mixtures that need fewer adhesives.
Understanding the Need for Decarbonization in The Construction Industry
Until recently, the construction industry’s response to reducing building-related emissions has focused on energy efficiency by reducing operational emissions – the energy used to heat, cool, and light buildings. This approach, however, overlooks the embodied carbon emissions associated with the material and building processes that occur throughout a building’s lifecycle. According to a study, the material product stage accounts for 62% of the total embodied carbon, the building use stage accounts for 24%, and the construction, demolition, and end-of-life stages account for 14% of the total.
Moreover, a recent report by the World Business Council for Sustainable Development (WBCSD) revealed that less than 1% of building projects currently assess or measure their lifecycle carbon impacts. The report outlines a path to reducing emissions from global building construction by 2030, with measurable and clear targets.
Since buildings are a significant contributor to emissions, it is critical that efforts increase to plan, monitor, and evaluate the entire lifecycle of materials used in construction.
The AEC sector can play a key role in combating climate change. The numbers are staggering: buildings account for 37% of global greenhouse gas emissions, comprising 27% in operational emissions and 10% in building materials and construction.
Being a sizeable industry with a substantial carbon footprint, construction cannot afford to wait. There is an urgent need for solutions to help accelerate the decarbonization of the built environment, aiming to limit the global temperature rise to below 1.5°C.
Decarbonizing construction is a process that has already begun and will ultimately result in this sector being subject to regulatory control. For instance, Vancouver, Canada, has mandated a 40% reduction in embodied carbon in new buildings by 2030, as part of its climate emergency response, demonstrating the type of regulatory framework that can drive market change.
Benefits of Decarbonizing Construction
The act of decarbonizing construction offers far more advantages than just environmental conservation, especially in the building sector. When we talk about decarbonizing construction, we are mostly talking about reducing carbon emissions in the building process—how much carbon a building emits during its construction, operation, and eventual demolition. But construction decarbonization can provide other benefits, too, and can be an enabler of building better buildings.
Decrease in the Environmental Impact
Decarbonization limits environmental damage and combats climate change. It achieves these aims by cutting the carbon footprint of construction work. Building materials and the means of construction must no longer depend on coal, oil, and gas. The process must become “low-carbon” or “carbon-constraining,” and has to be a part of what nature does. In other words, it has to use sustainable construction materials that come from renewable resources and must also minimize the use and disposal of construction materials to avoid building up a stock of them that ends up being a carbon sink.
Energy Efficiency and Cost Savings
Using less energy saves money. Programs that improve energy efficiency can save money and energy in the long run. To overcome the many different types of market obstacles to energy efficiency, they employ a broad variety of operational, equipment, and technological activities. Saving money and reducing the need for new power plants are two goals of national and local initiatives that encourage energy efficiency and the use of energy-efficient technology and practices.
Making the move toward decarbonization has a lasting impact on the energy efficiency of buildings. It’s one of the most effective changes we can make to reduce our overall carbon emissions. It yields not only lower operational expenses and energy consumption but also space that is healthier and more sustainable to work in. Energy savings from utility costs can be quite significant. And that is a promise that we can make when we boost our building energy codes to take advantage of good science and best practices.
Innovation and Technological Advancement
Advancements in technology and revolutionary ideas can work wonders. They are the lifeblood of corporations all around the world. Every year, businesses spend millions, if not billions, of dollars trying to come up with the next big thing, which will improve their bottom line or the world we live in. Furthermore, innovation and technological advancement, by their very nature, produce new jobs and new kinds of jobs. They are the spark that ignites the fire of entrepreneurship.
Building decarbonization is an exciting time for the building industry, and the construction of buildings is a large part of this movement. It is pushing the development of the use of sustainable building materials, digital construction technologies, and new techniques of construction. These materials and improvements allow for the utilization of much greener energies to be used in the construction and the lifespan of a building. Because today’s building decision-makers have an amazing palette of construction possibilities with which to work, they are also able to create by far the most energy-efficient, low-carbon, and net-zero buildings that have ever existed.
Health and Well-being
Decarbonization improves environmental quality and boosts occupant health and well-being by lowering indoor air pollution, increasing natural daylighting, and encouraging greater ventilation and thermal comfort. Healthy and more livable places are created by sustainable buildings, which are linked to decreased incidence of respiratory ailments, enhanced cognitive function, and more livable spaces for people to thrive.
Embodied Carbon Stages in Construction: Life Cycle Assessment
Tracking and reducing embodied carbon in construction is a challenging task. After all, every decision made in a project has an environmental impact. That is why companies are encouraged to follow various frameworks and methods to guide their efforts in the right direction. One of those frameworks is the Life Cycle Assessment (LCA).
The LCA is a structured method designed to evaluate the environmental impact of a product or building throughout its entire lifespan, from raw material extraction to disposal or recycling. LCAs are used for several reasons, including compliance with environmental regulations, client demand for information on the impact of projects, and in alignment with the company’s own goals of reducing emissions. Currently, LCAs are not mandatory, but they are increasingly required in green building certifications and EPDs.
The method, formalized in the 1990s, is governed by ISO standards 14040 and 14044, providing a strong framework for quantifying embodied carbon and ensuring that climate goals are based on transparent, evidence-based decision-making. The ISO standards outline a four-phase methodology for conducting an LCA: goal and scope definition, Life Cycle Inventory Analysis (LCI), where all relevant data is collected, Life Cycle Impact Assessment (LCIA), where data is translated into environmental impacts, and interpretation, where the results from the LCI and LCIA are presented and analyzed.
In Europe, LCAs for buildings commonly follow the EN 15978 and EN 15804 standards, which follow a modular structure that breaks down the project lifecycle in stages from A to D. For example, module A refers to upfront carbon emissions related to the construction or renovation of a structure. Modules B and C refer to “downstream” emissions, which are related to the usage and end-of-life stages of a structure or building. Let’s explore the modules in detail below!
A1-A3: Cradle-to-Gate
This lifecycle stage, known as Cradle-to-Gate, focuses on the production of materials and their processing and handling. It considers the extraction of raw materials, and all the processes involved, as well as the transportation and manufacture of those materials, until the moment they reach the factory gate, to be transported to the site. For example, suppose a building requires large amounts of cement. In that case, an LCA will help assess the emissions associated with extracting the raw materials, which in this case are limestone and clay (A1), transporting them to the factory (A2), and processing them into cement through various processes (A3).
- A1 – Raw material extraction
- A2 – Transportation of raw materials
- A3 – Manufacturing of building materials
To accurately measure the carbon emissions of materials through A1-A3, companies must rely on trusted data that is readily available. RIB CostX, a leading estimating and cost planning software, provides construction professionals with easy access to top carbon rate libraries, such as EC3 and 2050 Materials, to extract precise and up-to-date data to support and professionally estimate embodied carbon across all A phases.
A4-A5: Cradle-to-Site
The second stage, Cradle-to-Site, focuses on all the processes that happen on the construction site, starting with the emissions from transporting materials from the factory to the site (A4) and continuing with on-site assembly and installation (A5). It considers emissions from vehicles, machinery, and waste, providing teams with sufficient data to identify alternatives that reduce emissions through optimized routing, local sourcing, and efficient equipment use.
- A4 – Transportation to the construction site
- A5 – Construction and installation
Considering the importance and complexity of these processes, it is essential to support yourself with the right technology. RIB Candy, a powerful estimating and planning software, connects time and money into a single location to prevent miscommunications and data silos. Having cost estimating, subcontractor management, scheduling, and embodied carbon calculations, all in one platform, makes Candy a leading choice for industry professionals.
B1-B8: Operational phase
Also known as the “use” phase, it covers all aspects of the operational phase of a building or structure, including usage (B1), maintenance (B2), repair (B3), replacement (B4), and refurbishment (B5). Compared to the upfront emissions from the A stage, which are considered a one-time event, the emissions from B modules can span decades, making maintenance strategies and operational efficiency top priorities to reduce environmental impact.
- B1 – Use of the installed product
- B2 – Maintenance
- B3 – Repair
- B4 – Replacement
- B5 – Refurbishment
Stages B6 through B8 relate to the ongoing performance of the building and activities by its users. B6 and B7 capture operational energy and water use, typically classified as operational carbon rather than embodied carbon. B8 accounts for user-related emissions, such as commuting or equipment use, but is optional and often excluded unless explicitly defined in the project scope.
- B6 – Energy use
- B7 – Water use
- B8 – User-related emissions
C1-C4: Cradle-to-Grave
The C stage tracks all emissions related to the end-of-life process of a building or structure, including deconstruction (C1), transportation of waste (C2), waste processing, such as recycling (C3), and disposal (C4). This stage is critical as it provides the data to complete the full life cycle assessment, allowing teams to develop strategies to ensure the building is environmentally friendly, not only during construction and operation, but also in its disposal.
- C1 – Deconstruction and demolition
- C2 – Transportation of waste
- C3 – Waste processing
- C4 – Waste Disposal
D: Beyond the Life Cycle
Module D accounts for environmental benefits or burdens that occur after the product’s life has ended (outside the direct life cycle of the building). These might include the reuse of building components, recycling materials, or energy recovery. Module D was introduced by EN 15804, the European standard for EPDs, and while it’s not mandatory in the U.S., its use is expanding in voluntary reporting and comparative LCAs.
Methods like the LCA ensure engineers, architects, and entire construction project teams can assess the carbon emissions of a project across its entire lifecycle, allowing them to set target carbon reductions through material selection, design specifications, and operational efficiency.
The best strategy for measuring building carbon emissions is to start early in the design phase, as this allows for any necessary adjustments to be made to meet your carbon targets. Each element of the lifecycle, including materials, transportation, site activity, installation, and more, should be assigned an estimated carbon factor. The accuracy of the estimates will increase as more project-specific information is available, and new LCAs are conducted, especially after construction, to represent the “as-built” carbon emissions.
How Can Construction Decarbonization Be Accelerated?
To accelerate decarbonization in the building sector, a multipronged decarbonization strategy that integrates cutting-edge equipment, environmentally friendly procedures, and policy incentives is necessary. A low-carbon built environment can be achieved more quickly by using the following strategies, some of which are based on existing technology and practices.
To minimize the environmental impact, it is essential to use building materials with a smaller carbon footprint, such as substituting engineered wood products and utilizing concrete with lower carbon intensity.
When buildings are designed with energy efficiency in mind, they can minimize their operational carbon emissions. Important approaches include reducing the need for mechanical heating, cooling, and lighting systems, which incorporate principles such as orientation, insulation, natural ventilation, and daylighting.
We can achieve reduced heating and cooling costs by implementing a high-performance building envelope, which includes energy-efficient windows, insulation, and air-sealing techniques.
We can lessen our dependency on fossil fuels and mitigate operational carbon emissions by harnessing renewable energy sources to power buildings. Methods and technologies include renewable energy generation through the installation of solar photovoltaic (PV) systems, such as rooftop panels or solar facades.
To augment renewable energy production, small-scale wind turbines can be integrated into both urban and rural areas.
Decarbonization technology for “smart” buildings involves automating and digitally improving a structure’s functionality and energy efficiency. An example is building energy management systems, which track and adjust various building systems, including HVAC, lighting, and occupancy, to reduce energy consumption.
Recycling and reusing materials as much as possible, and reducing waste at every stage of a building’s lifespan, are two key goals of the circular economy. Among these are salvaging and reusing construction debris from demolition sites and establishing recycling programs to reduce trash sent to landfills.
By utilizing off-site manufacturing techniques to produce building components in controlled environments, prefabrication and modular construction can significantly reduce material waste and construction time.
Measuring Embodied Carbon in the Construction Industry
An effective way to reduce the impact of embodied carbon in new construction is to measure it. Only then can we compare, verify, track, and declare it with any degree of accuracy or governance.
In a recent report released by RIB Software, respondents were asked whether they have estimated the embodied carbon emissions related to their projects to quantify the percentage of respondents who have already begun the tracking process.
The survey unveiled a stark reality, with 70% of respondents not tracking embodied carbon in their projects. Among those who do, only 12% track it on a high number of projects; the rest do so in a low capacity. This indicates a critical gap in addressing one of construction’s most pervasive environmental concerns.
The full sustainable construction report from RIB can be accessed here.
For reasons like this, key players in the industry, including RIB Software, have partnered to sponsor Building Transparency’s Embodied Carbon in Construction Calculator (EC3), a revolutionary tool that is turning what has up until recently been an inexact science into an increasingly precise calculation method that helps to quantify and measure embodied carbon and its impact on building projects
Best Practices to Embed Sustainability into Your Construction Projects
86% of investors who were dissatisfied with the environmental risk information they received stated that disclosures in this area need improvement. With the increasing importance of sustainability in business, companies are under pressure, besides generating profits, to incorporate sustainability into their long-term decarbonization strategies.
Here are some first steps to consider:
- Develop a comprehensive long-term strategy that incorporates sustainability considerations throughout every process, from initiation to completion.
- Source materials ethically and ensure labor standards and fair humanitarian practices are considered in contractor and subcontractor management strategies.
- Implement sustainable design, engineering, and construction practices powered by relevant data to track, measure, and reduce emissions and waste throughout the project lifecycle.
- Use logistics processes that optimize deliveries to reduce mileage, emissions, and carbon footprint.
- Operate assets and equipment in an energy-efficient manner that is safe for the environment and for the workforce.
- Introduce technology in the pockets that are the root cause of emission blowouts, for example, carbon estimation and analyzing embodied carbon. Connect the teams via common tools and a Connected Data Environment to enable the elimination of emissions instead of their distribution, making emissions tangible rather than merely avoiding them.
Moving Towards a Net Zero Future
Here at RIB Software, we’re driven by disruptive digital technologies, best practices and trends, and have made it our purpose to propel the industry forward and make engineering and construction more efficient and sustainable. That includes supporting the development and availability of world-leading decarbonization software that empowers professionals to quantify, measure, report on, and compare embodied carbon across the project lifecycle.
Software like RIB Candy and RIB CostX can make a significant difference in the process by providing the necessary data and tools to accurately estimate the environmental impact of materials, design, and construction choices, and plan and implement strategies to effectively reduce them. Powerful collaboration features ensure teams are connected and can make decisions based on the latest information, increasing the efficiency, profitability, and sustainability of projects.
And we’re not stopping there; in-progress development sees our solutions ultimately enabling better design and procurement decisions, factoring in cost, time, and carbon to mitigate and eliminate embodied carbon used across the life cycle of a building.
Get your free demo today and experience the power of professional construction software solutions!
Most Recent
16 mins read
16 mins read
28 mins read
27 mins read
Blog Categories
Ebook