28 mins read
The Ultimate Guide to a Bill of Materials in Construction

It is a well-known fact that in construction, managing your project effectively is critical to completing your projects on schedule and within budget. To achieve this, one of the most important tools you must have in your arsenal is a well-prepared construction bill of materials (BOM). A construction BOM offers clarity, improves planning, and guarantees resource efficiency by clearly laying out the raw materials necessary for the project.
In this blog, we will explore exactly what a bill of materials entails, why it is so important to have a bill of materials, how to create an effective BOM, and much more.
Let’s delve in!
What is a Bill of Materials?
A bill of materials is a complete inventory of all raw materials needed for a construction project. It tracks resources throughout the project lifecycle, ensuring efficient execution, cost control, and quality management.
Bills of materials have been developed because of the necessity for planned and methodical building methods. By breaking down a project into its basic elements, a construction bill of materials allows for precise planning, accurate cost estimates, and optimal resource allocation. They are not just used in large-scale projects; they are also used in smaller construction activities ranging from erecting a single structure to installing complicated systems inside a building.
A bill of materials is used across a myriad of industries and includes:
- Raw materials (e.g. concrete, steel, wood)
- Quantities needed for each material
- Descriptions and specifications of components
- Costs and sourcing details
Bill of Materials vs Bill of Quantities

While a bill of materials (BOM) and a bill of quantities (BOQ) are both used to define and itemize requirements and costs, people often get confused about how they are used. These documents serve distinct purposes and are used at different stages of the project lifecycle.
A bill of quantities is a document that lists the items and quantities of work needed to accomplish a project. It consists of a description and a measurement that allows the job to be priced, and it is sent to contractors as a critical component of bid management in construction.
The project breakdown includes all building operations and tasks, such as determining quantities for each work item (e.g., cubic meters of concrete and square meters of flooring) and providing unit rates and total expenses for labor, materials, and other resources.
Quantity surveyor skills are often needed when preparing the bill of quantities, to assist contractors and customers in understanding the project scope, comparing bids, and managing budgets throughout execution.
In contrast, a bill of materials concentrates on the materials needed for the job, since the procurement and execution phases need a complete inventory of raw materials, components, and products required for the project.
In short: The bill of quantities includes providing accurate numbers and specs for each item, and providing supplier information, including pricing and delivery timeframes. The bill of materials guarantees that all supplies are purchased, transported, and ready for use throughout the project, avoiding delays and waste.
How They Work Together
The BoQ and BOM complement one another by addressing different parts of the project. Together, they help to improve planning, construction cost control, and overall project success.
By properly understanding the distinctions and utilizing the two documents effectively, construction professionals can speed up procedures, minimize risks, and execute projects efficiently.
Which Industries Use BOMs?
A bill of materials is not only used in construction but in various other industries:
Manufacturing: BOMs are used in sectors such as automotive, electronics, and consumer products to specify the components and subassemblies necessary for manufacturing. They promote assembly-line efficiency and quality control.
Technology & Software Development: Used to record hardware components (such as servers or devices) as well as software modules, assuring system compatibility and efficiency.
Retail and E-Commerce: Help with product bundling, packaging, and inventory planning. For example, they describe elements for bespoke packaging or customer-sold kits.
Healthcare and Medical Devices: Ensure compliance with quality and regulatory standards while producing medical equipment.
Pharmaceuticals: List the raw materials, chemicals, and packaging materials necessary for the production and delivery process, ensuring stringent compliance with regulations.
Energy and Utilities: Document materials and equipment in projects such as wind farms, power plants, and pipelines, ensuring that they are installed and maintained on schedule.
Food and Beverage: Include information on ingredients, packaging materials, and processing equipment required for effective production and packaging.
Shipbuilding and Maritime Construction: Arrange materials and components such as engines, hulls, and navigation systems.
These sectors depend on bills of materials to optimize procurement, maintain accuracy, and guarantee that projects or manufacturing processes run smoothly.
Types of Bills of Materials
Bills of materials vary in purpose and complexity. These are some of the types of bills of materials in construction:
A single-level bill of materials outlines the materials needed to produce a product or project. It is typically used for basic construction or manufacturing jobs that do not need sub-assemblies or complicated hierarchies. Single-level BOMs are simple to generate, interpret, and administer, making them excellent for small-scale projects with few dependencies.
A multi-level bill of materials is appropriate for complicated projects with several components and sub-assemblies. It depicts a hierarchical structure, outlining each layer of a project, from top-level assemblies to specific components. This type of BOM is crucial for large-scale construction projects or manufacturing processes where understanding the relationships between various components is essential.
During the design process, a construction engineers an Engineering bill of materials (EBOM) that comprises specified materials, components, and sub-assemblies. It focuses on design intent, which describes how the final product should be built and aligned with technical drawings or CAD files. EBOMs are essential for ensuring that design parameters are followed throughout manufacturing.
The Manufacturing bill of materials (MBOM) outlines all components, sub-assemblies, and raw materials needed for manufacturing. It offers extra information such as production instructions, machine settings, and tool requirements. MBOMs are essential for converting the concept into a workable plan for production teams, ensuring efficiency and precision on the shop floor or building site.
A Service bill of materials (SBOM) refers to a service. SBOMs are utilized for maintenance, repair, and operating purposes. It describes the components and spare parts needed to service or repair a product, which is sometimes accompanied by service instructions. SBOMs are essential for industries like construction equipment maintenance, where they can ensure timely repairs and extend the lifecycle of their equipment.
These types of bill of materials are designed for certain stages of a product or project’s lifetime, delivering crucial information to the right people at the right time. This allows for seamless construction site communication while reducing errors and inefficiencies.
What are the Benefits of a Bill of Materials in Construction?

A bill of materials in construction provides numerous major benefits that increase efficiency, accuracy, and cost-effectiveness in building projects. These advantages include:
Enhanced Planning
A detailed construction BOM improves project planning by accurately allocating resources based on items, quantities, and requirements. This degree of accuracy enables construction teams to anticipate and prepare for resource needs, considerably lowering the likelihood of material shortages or delays. It also improves scheduling and workflow management by allowing project managers to coordinate material delivery with project milestones.
Cost Control
A construction bill of materials helps teams analyze spending and find cost-saving opportunities by explicitly defining material requirements and pricing. Teams can prevent spending too much by exactly knowing material quantities and costs, which helps with construction budget control while improving financial predictability.
Efficiency
Another benefit is that it streamlines procurement management in construction by providing procurement teams with precise material requirements. It eliminates guesswork, decreases the need for last-minute purchases, and ensures that the correct supplies are delivered at the right time. This not only speeds up project schedules, but also avoids delays caused by missing or faulty supplies.
Improved Communication
This powerful document also serves as a common resource, improving construction project collaboration and communication among stakeholders, including architects, engineers, contractors, and suppliers. By providing a clear and consistent reference for material specs and quantities, everyone participating in the project is aligned and working toward the same goal.
Risk Reduction
A construction BOM minimizes the potential for errors by clearly defining material specifications, quantities, and requirements. This lowers the chances of overordering or underordering items, as well as the possibility of miscommunication or misunderstandings. Accurate material planning helps to minimize expensive rework, delays, and disputes, while safeguarding project timelines and budgets.
How to Create an Effective Construction BOM

Creating an accurate and effective construction BOM involves the following steps:
1. Define the Project Scope
Begin by precisely defining the project’s objectives, deliverables, and requirements. A well-defined scope lays the groundwork for your BOM by defining what needs to be accomplished and ensuring that all stakeholders have the same vision. This clarity helps to avoid scope creep and sets precise boundaries for the materials and resources you’ll need.
2. Break Down the Structure
Divide the project into manageable sections or stages. Breaking down the project enables you to concentrate on certain areas, such as the floor, department, or building phase, making it simpler to allocate supplies and check progress. This systematic method allows for better resource allocation and identifies possible difficulties early on.
3. List all materials
Create a complete list of all raw materials, components, and tools needed for the job. From structural components to finishing touches, make sure that no detail is ignored. A complete list not only allows for precise budgeting but also eliminates delays caused by missing materials.
4. Specify quantities
Determine exactly how much of each material you require. Use detailed measurements, engineering plans, or expert consultation to calculate precise quantities. This stage is critical for minimizing excess and shortages, which may result in budget overruns or project delays.
5. Include descriptions
Specify and describe each item on your list in detail. Include technical specifications like size, quality standards, and manufacturer information. Detailed descriptions guarantee that everyone, from suppliers to on-site workers, knows precisely what is expected, reducing miscommunication and mistakes.
6. Factor in Costs
Create a realistic budget by including current pricing and sourcing information for all items. Understanding the cost implications of each item allows you to better manage your spending and predict possible price swings. This transparency is key to maintaining financial control throughout the project.
7. Review and validate
Before finalizing the BOM, conduct a thorough review to ensure accuracy and completeness. Engage team members from different departments to help verify the list. This collaborative process helps to identify any oversights and ensures that all aspects of the project are addressed, resulting in a more reliable and effective BOM.
8. Use modern software
Leverage modern material management tools like RIB Candy to streamline the process. Such software can automate difficult calculations, update pricing in real time, and provide useful data about your material needs. Integrating digital technologies not only saves time but also improves accuracy, turning your BOM into a dynamic resource that changes as the project progresses.
Final Thoughts
A well-prepared bill of materials is a critical component of every successful construction project. By giving a clear roadmap of materials, quantities, and specifications, it improves planning, cost management, efficiency, and communication, ultimately leading projects to completion on schedule and under budget. Whether for procurement, inventory management, or execution, this document guarantees that every resource is properly accounted for, eliminating waste and risk.
However, generating and managing a BOM manually may be challenging, error-prone, and time-consuming. This is where digital solutions like RIB Candy come into play. Our solution is a cutting-edge estimating and project management software that automates BOM development, construction cost estimation, and procurement, reducing inefficiencies and providing unparalleled control over your building supplies.
Ready to elevate your bill of materials and ensure a smooth project execution? Discover how RIB Candy can transform your construction processes – get your free product demo now!
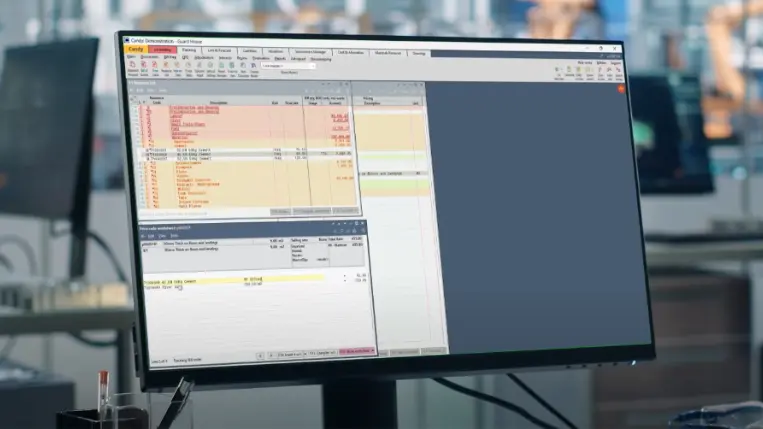
Most Recent
28 mins read
27 mins read
24 mins read
25 mins read
Blog Categories
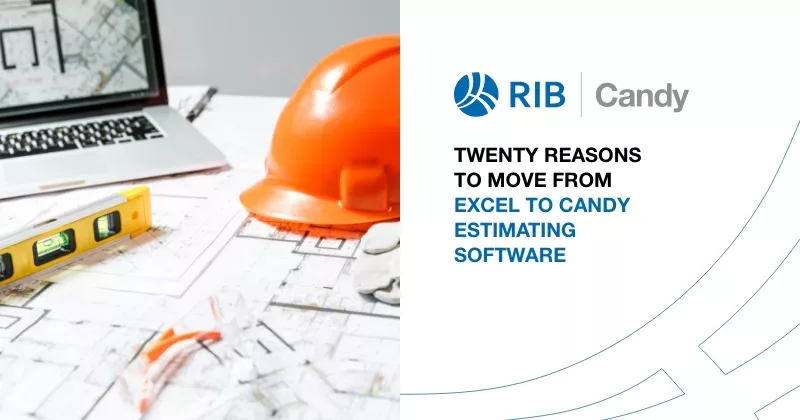
Ebook