6 mins read
Stubbe’s Precast – a iTWO PPS Success Case
4 mins read
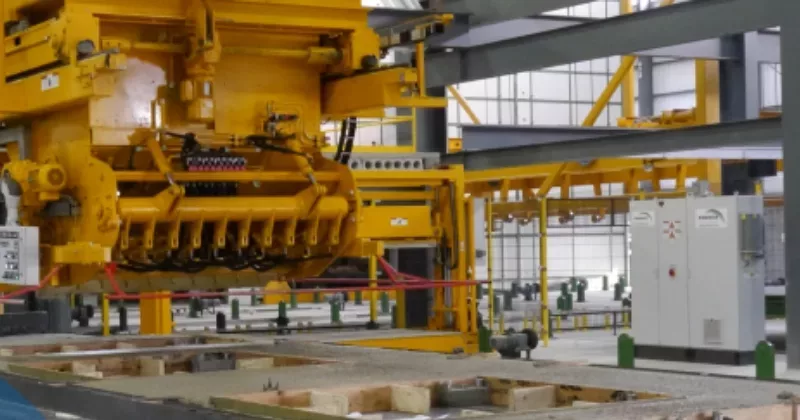
Stubbe’s was founded in 1982 by Herb Stubbe, when he designed and manufactured the first precast concrete hog feeders in Ontario, Canada. Today Stubbe’s is a large precaster in North America that produces a variety of (precast) concrete products for the agricultural, residential, commercial and industrial markets. Precast production takes place at four manufacturing plants in Southwestern Ontario. In 2016 Stubbe’s started up a state of the art, 200,000 square feet, wall plant utilizing a 3-lane carousel system.
Strategy and Goals
| Continuously challenging the norm and looking for innovation and process improvements.
| Fully utilize capacity.
| Protect the business by vertical integration and diversification
| Optimize and digitize internal processes to increase visibility in business performance
Challenges
| Short term and long term visibility into performance of the various parts of the business became more and more challenging
| Coordination of all aspects of the jobs required more and more people for planning and scheduling. With continued significant growth this became more and more challenging.
| Planning via excel spreadsheets became more and more difficult and showed the need for a scalable and user friendly software system that addresses the precast specific requirements in an efficient manner.
Solution
Stubbe’s has the whole Smart Production product family in use. In the state-of-the-art automated precast circulation factory they are using iTWO MES in combination with a bundle of high automated iTWO ICS robot and machine systems. Effective in 2021 the iTWO MES system is also being used for the conventional long bed planning/nesting in the Wetcast and Hollowcore plants. On top of that the whole project- and utilization-planning and the transport planning is done with iTWO PPS.
Outcomes
| Significantly improved visibility for Long Term and Short Term Capacity planning
| Piece tracking has become much easier. We are not forgetting to produce items or double producing them. Tracking our product in our massive yard has become much easier resulting in wrong product being shipped to site almost non-existent
| Combining data from iTWO PPS with data from our Detailing/Engineering software, Accounting system and Quality system has greatly helped us with not only analyzing data, trends, costing etc. but also helps us look ahead for material usage, planning and scheduling requirements for supporting departments etc.
| The iTWO installation planning board has greatly improved the visibility on crew utilization and where there are openings for jobs to be slotted in.
| By modifying the MES to suit the nesting of Hollowcore and other long bed production, all production scheduling is now running off the same system.
| We are slowly working away it reducing paperwork and replacing it with digital copies.
| Adding new plants over time has been relatively seamless
“We started implementation of the PPS system in 2015. The PPS system has greatly enhanced our ability to schedule and track the large number of products to be produced across hundreds of projects. The data from PPS combined with data from Engineering, Accounting and Quality helps us in providing visibility of future capacity utilization and potential over- or underbookings for our sales, engineering, production and installation teams, as well as forecasted material use and real time costing. PPS has been instrumental in providing a platform to handle the growth of our precast division. ”
– Henk Van De Ridder, Vice President of Corporate Service, Stubbe’s – |
Most Recent
6 mins read
8 mins read
6 mins read
4 mins read
Case Study Categories
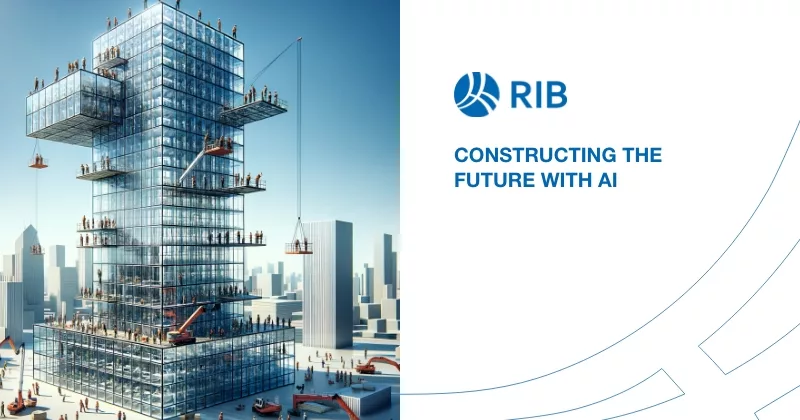
Ebook