7 mins read
Towards A Greener Construction Industry: Starting Small, Thinking Big, Scaling Fast
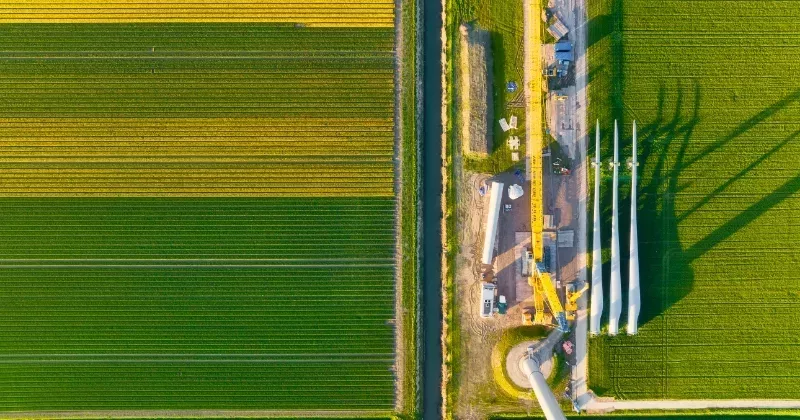
September 2022
While the construction industry is responsible for about 40% of carbon emissions, its project-centric nature means it is uniquely placed to drive the green agenda and adopt measures that ultimately turn the tide on global warming, writes RIB Chief Strategy & Marketing Officer, Mads Bording.
Decarbonisation of the construction industry is a complex undertaking. Before the construction process begins, the embodied carbon or CO2e emitted in producing materials such as steel and concrete needs to be considered. This includes the extraction, transportation, refining, manufacture and implementation of materials such as steel and concrete.
A raw material such as iron ore, for example, needs to be refined before it can be used to create construction materials. Once iron ore has been extracted from the ground, a process that requires the use of heavy industrial machinery, it is transported (often long distances) to a steel mill where it is smelted, shaped and transported yet again.
Next, it needs to be converted from a purified raw material into something that can be used in the construction process such as a sheet of metal, rebar or steel beam with specific dimensions, and then transported again. Each of these processes requires significant energy and resources. And, this is before the steel can be placed into a concrete slab or used for a construction project.
Then there is the actual execution of a construction project on site. This is often where poor planning comes into play, with the majority of projects experiencing between 20% and 30% in cost overruns, mainly due to defects, rework and missing information. In addition, the construction process generates waste, which needs decommissioned or sent to landfill.
While this is largely how the industry works today, global sustainability goals are compelling construction companies and other industry players to measure their CO2e footprints and consider using greener building materials such as concrete with 30% less CO2e, cross-laminated timber and other smart building materials. These, however, may need longer curing times (concrete) or be more expensive to manufacture and use.
This, in turn, requires greater collaboration and more advanced planning tools. These tools allow for location-based planning or tagged planning, which takes the longer queuing times into account.
Another option is to simulate a project, not only from a time and cost point of view, but also from an embodied carbon perspective. When a project is simulated, it is possible to identify the harmful materials. And, if integrated software is used, project managers can find ways to mitigate these, such as changing materials or suppliers – in the same way one mitigates a financial or schedule risk.
Of course, by changing the mix to reduce embodied carbon, there will be an immediate cost and time implication. That said, public sentiment and new legislation is dictating that players in the construction industry think and act differently, and make trade-offs to ensure their carbon footprints are as low as possible.
In Nordic countries, for example, penalties apply if a LED certificate is not produced for a new or retrofitted building. And, this is becoming more stringent as buildings are beginning to be taxed based on their lifetime energy consumption. Leading the way in this, Singapore has hiked up taxes on buildings in relation to their CO2e emissions.
There have been instances where project owners have mandated the use of certain materials, but when the project has been handed over to general contractors, they have swapped the good material for something cheaper.
Today, general contractors in some countries have to clearly account for everything that goes into a building. If they cannot do so, they can incur a tax penalty of up to 25%. Given that typical project margins are between 5% and 12%, they end up losing money on the project. While this currently applies to greenfield projects, the same is expected to come into play for retrofits and refurbishments.
Upcycling and the reuse of materials such as concrete and plastic is another emerging trend. One company specialises in cutting out pieces of concrete from old commercial buildings for use in residential projects, extending the lifecycle of the material and minimising carbon emissions.
Importantly, technology is the pivot point for these endeavours as it enables decisions relating to material choices and creates the visibility that is necessary for different players – architects, engineers, contractors – to collaborate in meeting client requirements.
If a client wants a sustainable building with greener material, there needs to be some way to measure the impact of this down the line. Sustainability needs to be factored into construction company business models to ensure greater profitability when using building materials that have less embodied carbon.
As with any emerging mega trend, there needs to be an audience and a burning platform. And no burning platform can be more compelling than the planet becoming five degrees hotter. As a species, we need to find a way to stop this trajectory before it gets worse. We need companies to pledge to achieving carbon net zero status like Microsoft has done. And, this needs to correlate with share prices.
When consumers and businesses drive the green agenda, they promote the creation of lighthouse examples that resonate with others, examples that transform an evolution into a revolution, examples that compel the slow-to-change construction industry to start small, think big and scale fast.
Most Recent
7 mins read
3 mins read
5 mins read
5 mins read
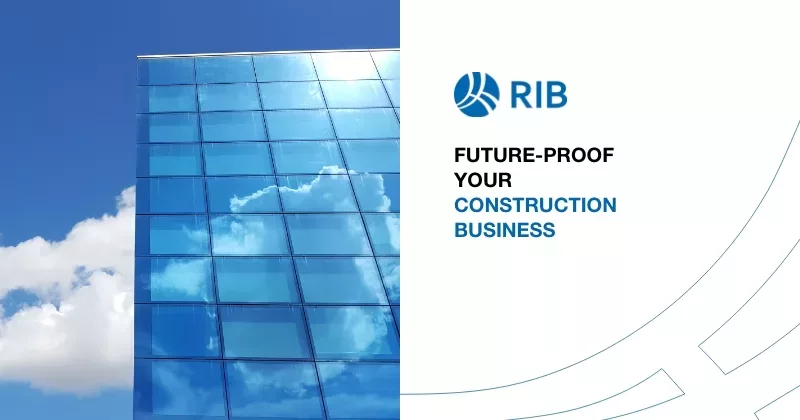
Ebook